What is RFID: The meaning behind the technology?
RFID (radio-frequency identification) is a wireless tracking technology that uses radio waves to identify and track objects. RFID technology uses RFID tags, which are mounted on objects. RFID tags consist of a microchip that can store data and an antenna that can transmit data to an RFID reader. The RFID reader then captures the transmitted data and sends it to a computer system for processing.
You may experience that RFID technology often is confused with barcode technology. However, it is different and has significant advantages over barcode technology as it can read multiple items or products at the same time and still distinguish between individual items, enabling accurate asset tracking. Unlike barcodes on products, which normally use a GTIN (Global Trade Item Number) to identify a type of product, RFID tags use a SGTIN (Serialized Global Trade Item Number) to identify and track individual items at the same time. Using barcoded SGTIN, on the other hand, requires the individual scanning of each item barcode, which is time-consuming.
For example, 100 branded T-shirts in a clothing store will have the same GTIN so, when a T-shirt is scanned, the reader can identify the brand and type of T-shirt, however it is not able to distinguish one of the T-shirts from another. By using RFID tags with SGTIN, all 100 T-shirts are identified individually and together at the same time, meaning the brand and type of T-shirt is recognized. This enables businesses to track individual items and capture specific, valuable data about them, such as product information, country of origin and best before date, which can be stored in the RFID tag and transmitted to a reader, and subsequently processed by a computer system. Importantly, in this example, RFID scanning of all 100 T-shirts takes a few seconds, whereas barcode scanning of the same 100 items takes a few seconds per item of manual labour time. The efficiency gain using RFID is huge.
RFID tracking technology has revolutionized asset tracking and inventory management in many industries, including the airports and airlines, healthcare, postal and supply chain sectors by providing accurate, real-time data about products and assets.
How RFID technology is revolutionizing supply chain management
In the supply chain and logistics industry, asset tracking and management faces several challenges. One of the most common problems is the lack of real-time visibility across the entire supply chain, which can lead to delays, mis-shipments, disruptions and loss or theft of valuable assets, impacting companies’ reputations and causing significant financial loss. Manually locating assets is extremely time-consuming and costly, and increases the risk of human errors, which can result in inaccurate data, inefficiencies and delays in the supply chain.
Businesses are increasingly turning to RFID location tracking technology to optimize asset and inventory management. RFID enables automated data capture and tracking of goods, which reduces the need for manual processes and therefore the likelihood of human error. With RFID, you can quickly and accurately locate assets, track inventory levels, and monitor the movement of goods in real time or near real time. This improves the inventory accuracy, enhances workflow efficiency, reduces variable costs and, ultimately, enhances customer satisfaction. RFID technology has proven to be a game-changer for the logistics industry, enabling businesses to achieve greater visibility and control over their supply chains, which normally results in improved efficiency, cost savings and better customer service.
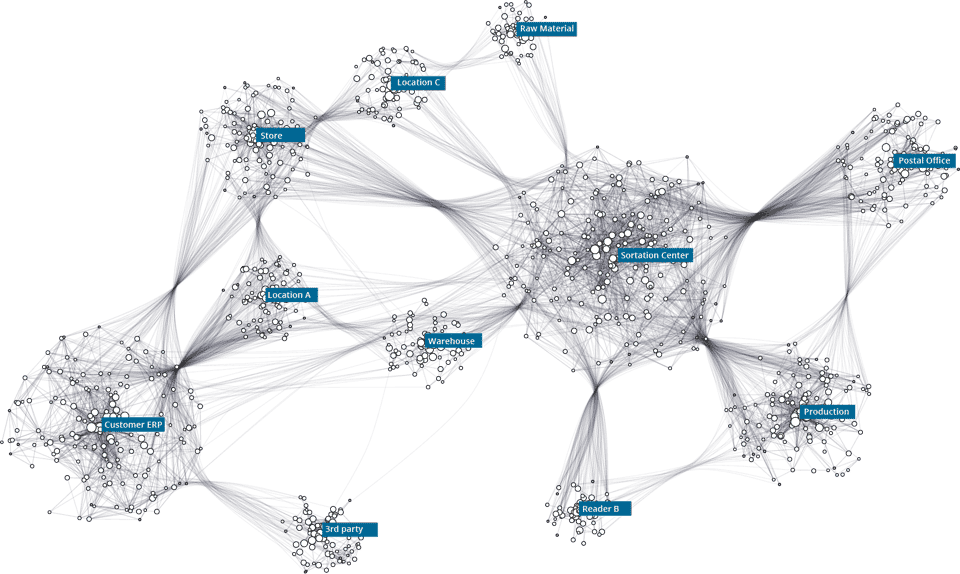
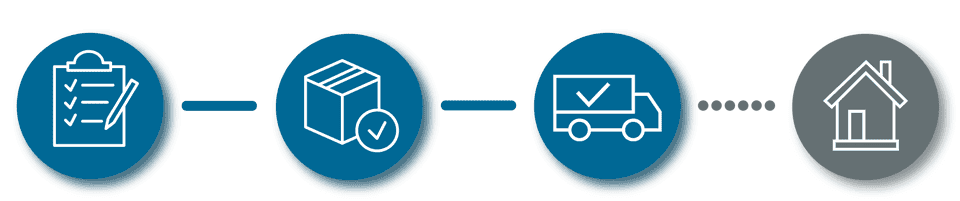
RFID tags enable full visibility and traceability of your logistics and supply chain
The manual scanning of goods can be prone to errors caused by human mistakes, misreading's or poor scanning compliance, which can easily result in visibility gaps and subsequent inaccuracies and delays in the supply chain. There are endless ways in which this can occur, for example, an individual may forget to scan an item or container, or a ULD (unit load device) may arrive at a depot via the wrong door. This can lead to inaccurate inventory levels and delays in processing orders, which can create inefficiencies and impact the customer experience.
The use of RFID technology mitigates these risks by providing an automated scan, which registers the item or container at a choke point, such as an RFID gate, at a handover stage within the supply chain. This not only achieves a higher scan performance (i.e., quicker and more accurate), providing visibility throughout the supply chain, but it also reduces variable costs, such as labour.
Transforming Libraries with RFID Technology
In the realm of libraries and information management, the challenge has always been in optimizing the handling and tracking of physical books and assets. Traditionally, libraries relied heavily on manual methods, mainly barcoding, for tracking. However, these methods, while functional, often come with the pitfalls of human error, misplaced tags, or misorientation of codes, leading to inefficiencies in check-ins, check-outs, and inventory management.
Turning the page to modern solutions, libraries globally are now embracing RFID technology. RFID offers libraries a precise, automated method to track assets in real-time. With RFID, gone are the days of incorrectly placed barcodes; the technology reads tags regardless of the orientation of the book or item, simplifying processes for both staff and patrons. This not only streamlines asset handling but also bolsters security, ensuring that only properly checked-out items leave the premises.
Moreover, with the integration of self-service kiosks, such as those provided by Lyngsoe Systems, patrons are granted autonomy. They can manage check-outs, renewals, and returns, reducing staff intervention and increasing overall efficiency. This empowerment translates to a more satisfactory user experience, as patrons can handle processes at their own pace, and librarians can better allocate their time towards more value-added services.
In essence, RFID technology is heralding a new chapter for libraries. It’s offering them a more efficient, error-free, and user-centric approach to asset management, security, and patron services. With institutions like Lyngsoe Systems at the helm, the literary world is set to be more interconnected, secure, and responsive to modern challenges and user needs.
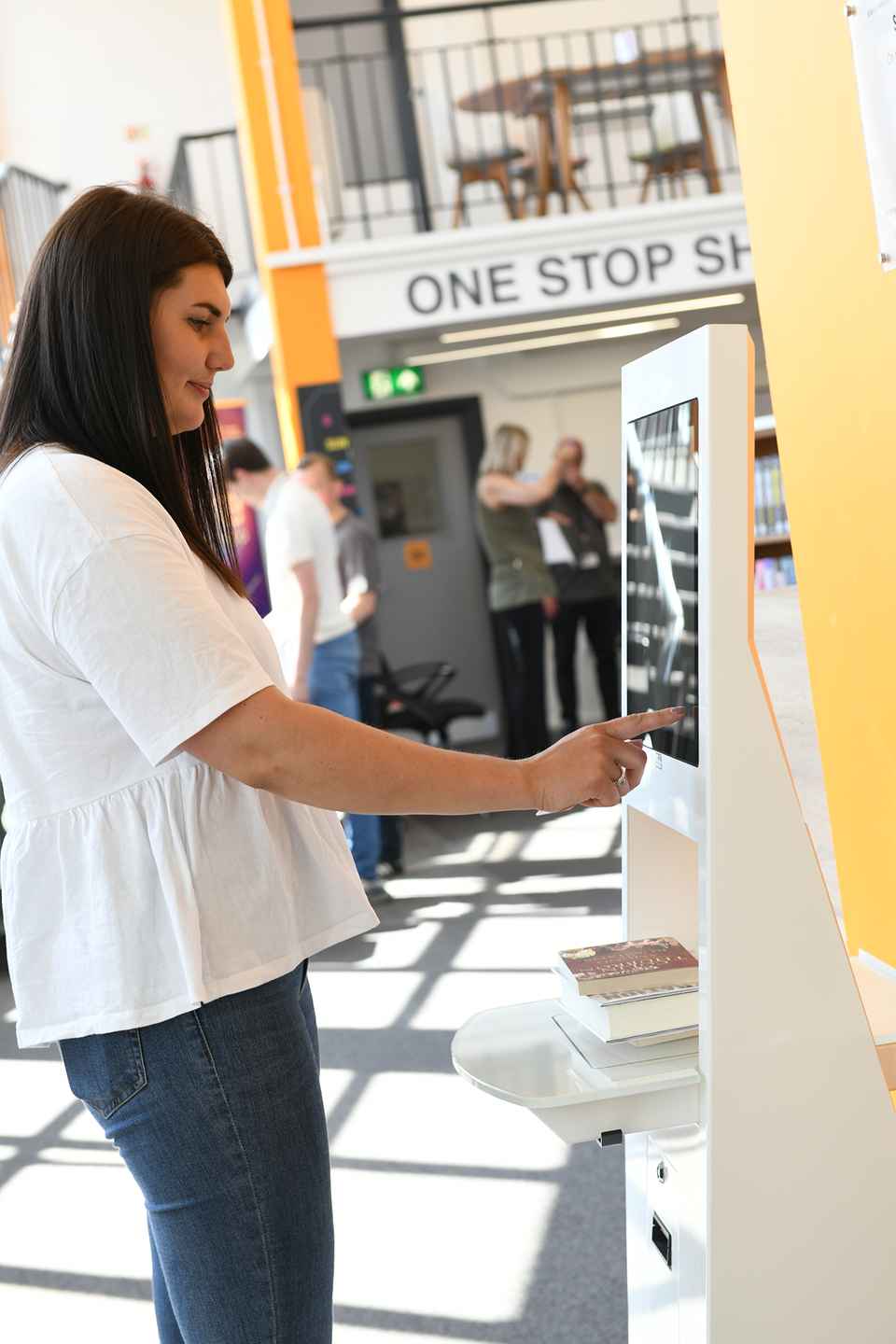
RFID technology in healthcare: Improving patient care and safety
RFID tracking systems are increasingly being used in the healthcare sector to optimize asset and inventory management, as well as improve patient safety and care. At Lyngsoe Systems, we provide many uses of RFID technology in healthcare, including the tracking of medical devices,hospital beds, sterile goodsandsafety equipment.
By using RFID technology, hospitals and healthcare providers can improve maintenance and cleaning management, ensuring medical equipment is fit for use, which helps reduce the risk of infection and injury. It also helps to improve asset utilization and operational efficiency, as healthcare professionals can more easily locate and access necessary medical devices, saving valuable time and reducing delays and cancellations of treatment and procedures. In addition, RFID technology can help hospitals better manage patient flow by tracking the location of hospital beds and equipment, which can help reduce wait times and improve patient care and satisfaction.
Lyngsoe X-Tracking™ – Keep track of valuable assets and equipment in real time
Lyngsoe X-Tracking™ is a GS1 certified, cloud-based, front-end solution that enables businesses to accurately track their assets and equipment in real time or near real time. The solution is used in a variety of industries from manufacturing and logistics for the tracking of containers and products, to museums and galleries for the tracking of valuable assets, such as paintings.
X-Tracking™ has a user-friendly application where our customers can see the location of all labelled assets in a list or on a virtual map, as well as the status of assets, such as whether a ULD, trolley, roll cage or tray is full or empty, or whether a device requires repair or maintenance. This allows you to easily locate and control assets in the supply chain or across multiple locations, set up read points in key locations and create rules and alerts, such as a notification when an item is due for planned preventative maintenance (PPM).
Using RFID and other technologies, including BLE, Wi-Fi and GPS, X-Tracking™ removes manual processes, such as barcode scanning, and replaces them with automated processes. For example, when an asset is moved from one location to another, it is automatically scanned and registered, updating the X-Tracking™ user interface in real time or near real time.
X-Tracking™ is easy to set up and integrate with third party applications, such as ERP systems and asset management platforms. It is highly customizable and scalable, allowing you to tailor it to your specific needs. Working with Lyngsoe LIVE Logistics™, X-Tracking™ forms a powerful tool for improving asset tracking capabilities and streamlining operations.
Leading the way with real-time tracking and traceability
Lyngsoe LIVE Logistics™ is a back-end software platform that, along with X-Tracking™, forms part of a comprehensive solution for businesses with logistical challenges. The software processes captured data into meaningful events and sends them to X-Tracking™, as well as third party platforms, such as ERP systems. Its API can integrate with any existing application, making it a flexible solution for businesses of all sizes across all sectors.
The platform is cloud-based, enabling you to access it from anywhere, at any time. It can process and filter data from various data sources, making it a versatile solution for businesses with diverse inventory management needs. Additionally, Lyngsoe LIVE Logistics™ has advanced algorithms and analytics tools that enable you to identify trends and patterns in your inventory and logistics data, allowing you to make informed decisions and optimize your logistics processes.
If you are in the market for Bluetooth Low Energy (BLE) and RFID tags for logistics optimization you may read more about the technologies at Lyngsoe Systems or contact us for more information.
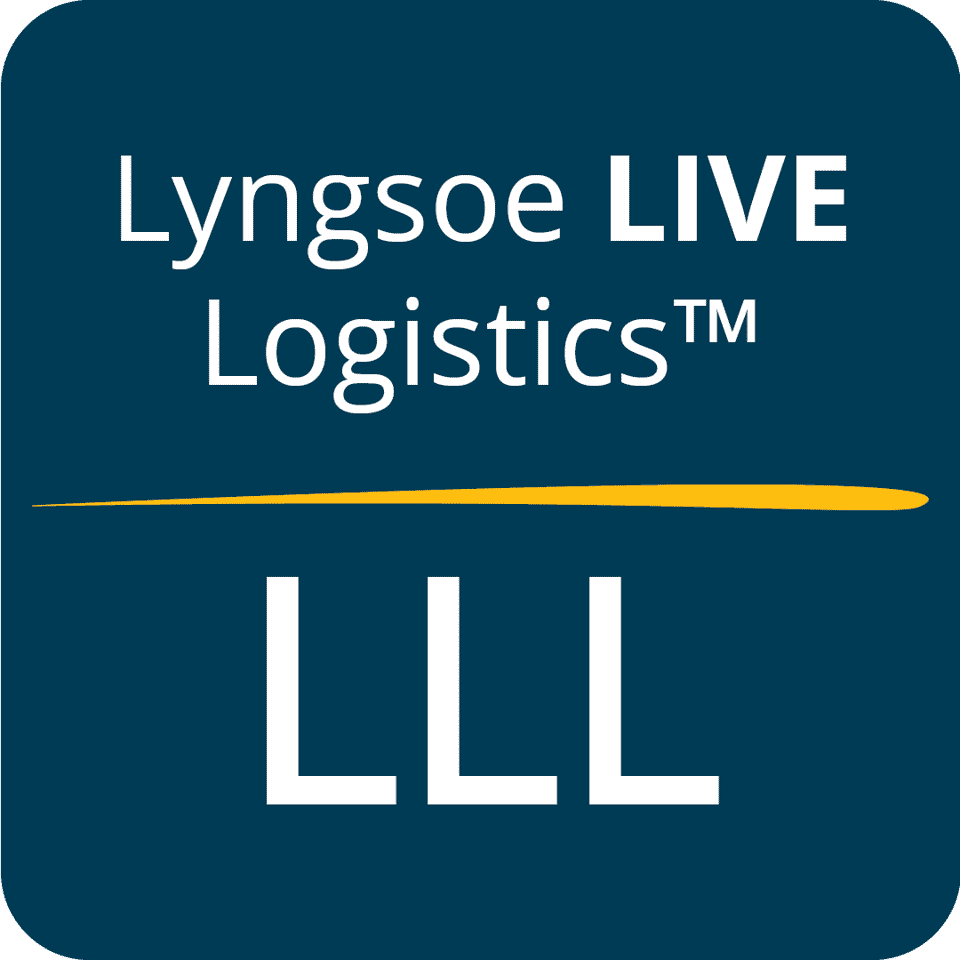
How we helped Pack and Sea A/S gain full visibility and traceability of important assets
Pack and Sea A/S is a Danish company that provides packaging, logistics and transport solutions to businesses across Europe and around the world. The company faced a high-cost problem – locating 400,000 fish crates, which were often misplaced or lost, across multiple fishing ports.
At Lyngsoe Systems, we worked closely with Pack and Sea A/S to implement a returnable transport asset (RTA) tracking system using X-Tracking™ and Lyngsoe LIVE Logistics™. The RTAs, such as crates and containers, were fitted with RFID tags that were scanned at various points in the supply chain, providing real-time visibility of the location and status of the assets. This enabled Pack and Sea A/S to reduce the number of lost assets and improve its maintenance and replacement planning, resulting in significant cost savings and improved efficiency of its logistics operations.
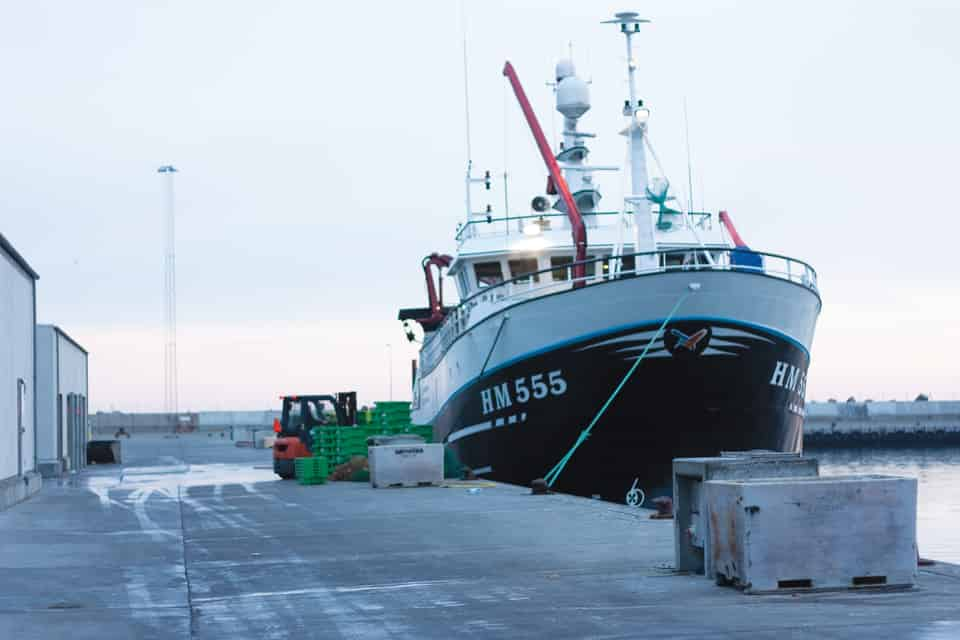
Active vs. passive RFID technology
How each solution benefits your business
Activeand passive RFID tracking tags are two types of tags used for RFID asset tracking. The primary difference between the two is that active tags have their own power source, while passive tags rely on power from the RFID reader. Active tags have a longer read range and can provide additional functionality, such as monitoring light, movement and humidity. However, they are more expensive and require regular battery replacement. Passive tags are more cost-effective and have a longer lifespan, but they have a shorter read range. We can advise you on the most appropriate RFID tag for your specific needs.
Scale your tracking capabilities with active RFID
Active RFID supports growing logistics requirements and complex tracking environments. Learn about our leading active RFID solutions now.
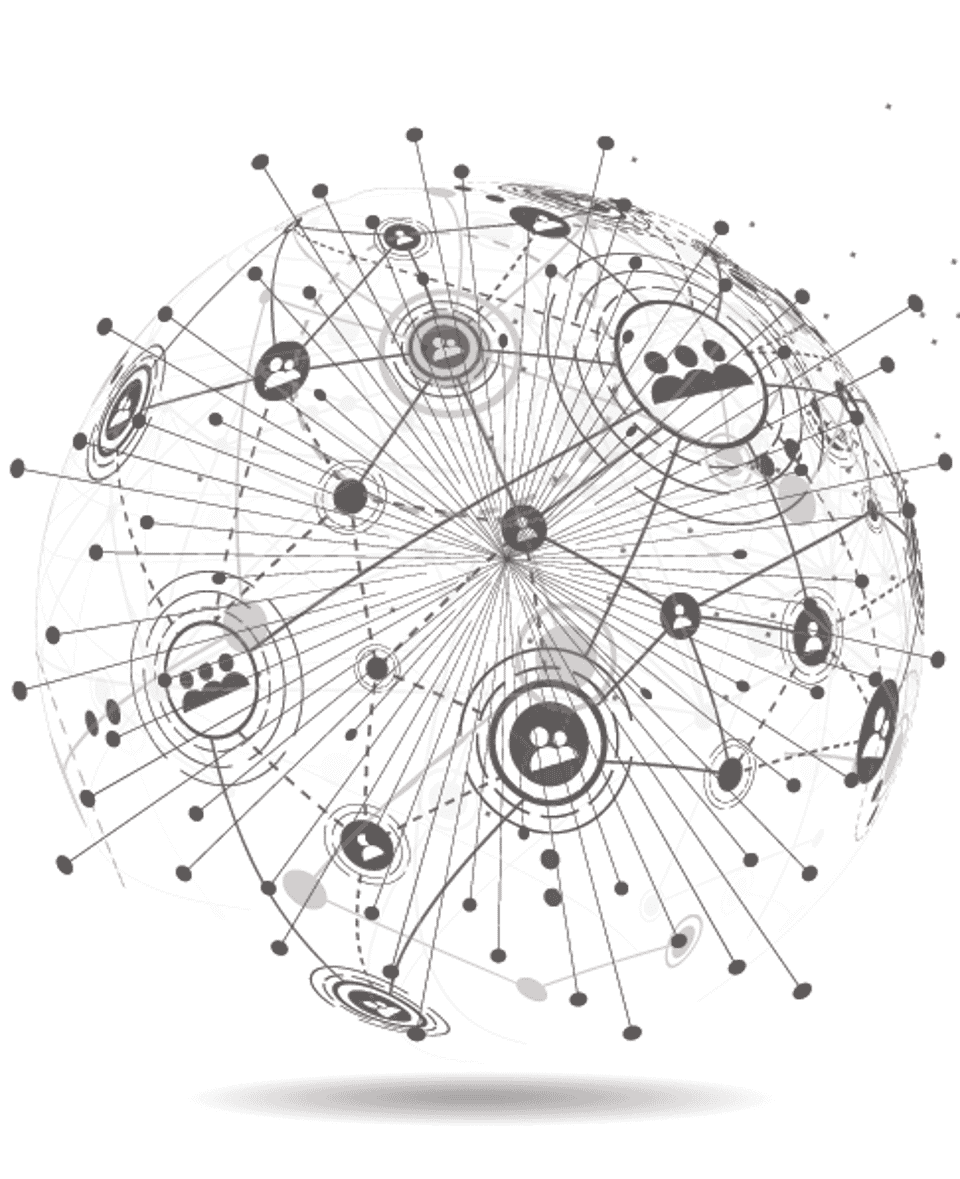
Keep track of inventory and assets with passive RFID tracking
Passive RFID helps you gain real-time traceability and visibility. Learn more about our passive RFID tracking solutions at Lyngsoe Systems.
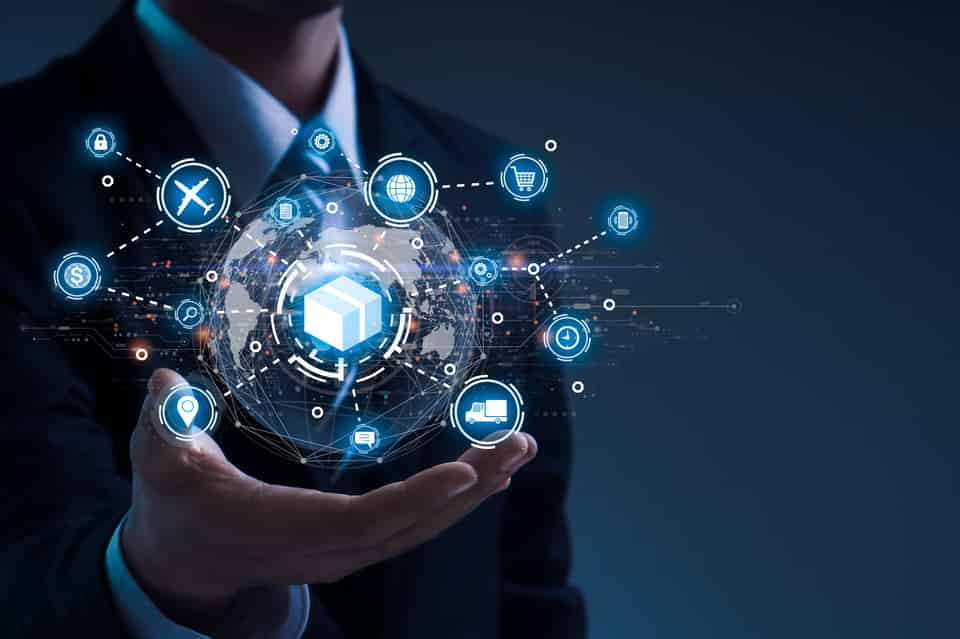
Lead the way with RFID tracking technology
At Lyngsoe Systems, we are leaders in the field of RFID tracking technology with a strong focus on developing the right solution for each customer. Our technology agnostic solutions are designed to help you improve your inventory management, asset utilization, operational efficiencies and customer experience.
Speak with one of our experts to find out more about how our asset tracking solutions can transform your logistics operations.
FAQ
How does RFID differ from barcode technology?
Unlike barcodes, which require line-of-sight scanning and identify product types, RFID can read multiple items simultaneously without direct visibility and can uniquely identify individual items.
What components make up an RFID system?
An RFID system consists of RFID tags (attached to items), RFID readers (to capture tag data), and a computer system to process the information. RFID tags can be passive (without a power source) or active (with a battery), each suited to different applications based on range and data requirements.
In which industries is RFID commonly used?
RFID is utilized across various sectors, including airports and airlines, healthcare, postal services, and supply chain management, for asset tracking and inventory management.