Case Story: Aarhus Public Libraries
Real-Time Automation Delivers Efficient Service to Communities
“I see a big future in handling curated displays, it takes a lot of intellectual work to find the connection between different titles, but I like the concept of an intelligently managed, reusable exhibition with a clear line of subject, author, category or whatever else the library would like to promote.”
Anders Nørregaard of Aarhus Libraries
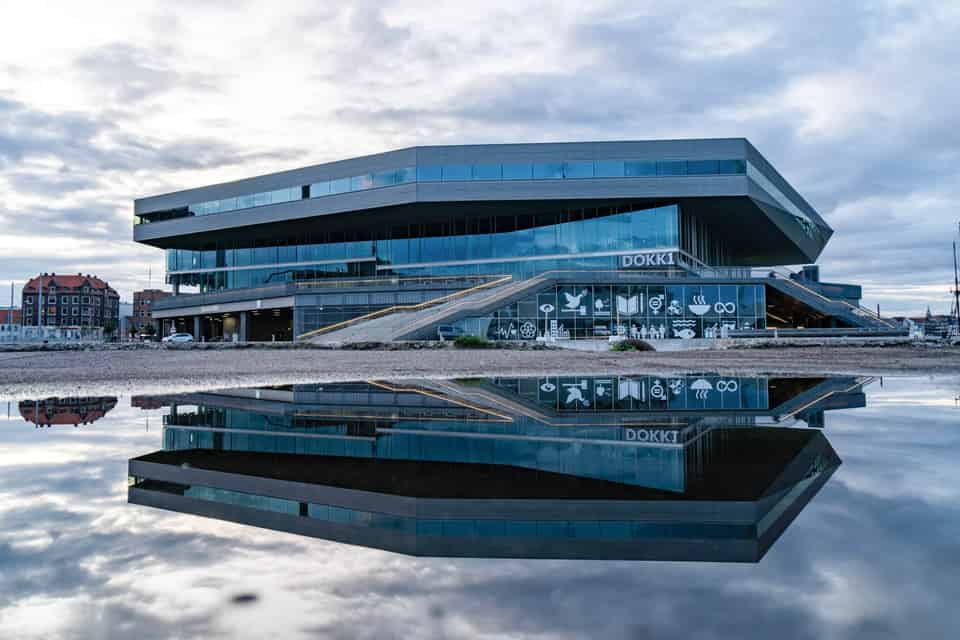
About the Library
- Aarhus is the second-largest city in Denmark with 310,000 inhabitants.
- Aarhus Public Libraries consists of the main library at Dokk1 and 18 branch libraries.
- The library at Dokk1 is a center for knowledge and culture which disseminates and makes a wide variety of media available and come alive across all genres and formats. The library is the citizens’ house. Staff and management of the organization continually work with public involvement.
- In 2009 staff at AAKB started the NEXT LIBRARY® conference and network series. This is an international gathering of forward-thinking library professionals, innovators, and decision-makers who are pushing boundaries and making changes that support learning in the 21st century”, with more than 1400 librarians from 96 countries in its network.
- Created by AAKB and first presented in 2009, the NEXT LIBRARY® events look ahead and explore the continuously evolving nature of the public library in the 21st century. It is an international gathering of forward-thinking library professionals, innovators, and decision-makers who are pushing boundaries and making changes that support learning in the 22nd century.
The Challenge
Looking for a solution
In 2010, as the number of staff at the Aarhus Public libraries had been halved and the library was altering the focus of its work, the Aarhus and Copenhagen Public libraries teamed up to bid for a smarter material handling system. The libraries had different pain points, but it was imperative to solve the continuing conflict between cuts to staffing levels and the need to increase library activities.
The main focus from Aarhus Public Library (AAKB) was to introduce a fully floating collection with all the benefits it would give in the form of a better distributed collection, less transport, and fewer copies while ensuring that there were none of the drawbacks as seen from other library systems – such as pooling and depletion in branches and the time-consuming rebalancing of the collection – “it was just not going to happen”. Statistics at the time showed a strong net flow from the Central Library in the center in town with returns in smaller branches in residential areas.
At the time discussions ran high – it was clear that for floating collections to REALLY work some sort of automation was required – but what about the branch librarians’ heart blood, the book selection for THEIR users? Floating the collection might drain the carefully selected titles to other branches, maybe never to appear again. What about the precious children’s books seeping out to the branches where the more computer-savvy parent lived?
Automatization and change management were not new concepts to the staff at Aarhus, as they had been automating and changing workflows from the early 90s.
The first introduction of self-service stations taught the library much about the necessity of staff involvement to ensure that large technical workflow changes are successful. Therefore, the decision and procurement process of one of the very first central sorters in Denmark was led by staff and the sorter eventually got constructed by FKI Logistex in 2002. Lyngsoe Systems acquired the FKI Logistex library solutions in September 2009 and indeed some of the very early engineers on this first central sorter for libraries are still with the company.
Susanne Hansen describes the process of building such an (at the time) innovative Automated Material Handling system as both challenging and exciting: “I think, I worked 24 hrs a day, every day that first year and I learned how to use a screwdriver and indeed about who from the staff I could trust to use one”.
The first AMH got replaced with a large 100-bin sorter from PV Supa (now part of Lyngsoe Systems) when in 2016 the library moved to the beautiful new DOKK1 on the Aarhus harbor front. It was immediately clear that the new, next-generation sorter was a blessing of much less noise and it was much easier to clean and maintain.
“The introduction of the sorter and self-service returns led to extensive change of workflows throughout the library, simplifying material handling leading to a drastic fall in work related injuries from afflicting almost 100% of the circulation desk staff to 0%.“
“That IMMS™ runs on generic Android smartphones makes a big difference. All staff have the IMMS™ app on their mobile phone, so all daily tasks such as registration, picking and correcting errors, can be done ad hoc when and where there is a little time.”
Carsten Hammershøi
Aarhus Libraries
The Solution
Learning from other industries
However, issues also arose from the first automation: When a reserved book was returned to the shiny new FKI sorting machine, patrons got notified automatically by the ILS, which led to confusion and lots of time spent looking for material still on its way to the shelf. Years later this led to a clear requirement for the IMMS™ development: a proper track and trace system was needed with notifications not going out before an item was shelved on the actual reservation shelf.
With this strong history of automation, the library was very clear that if float should be a success, they needed to automate the handling and embrace the new routines fully. If not the envisioned benefits would never be achieved.
During one week of the summer of 2010, staff in select branches performed basic time measurements, jotting down on paper whenever material was handled – from basic processes like shelving and tidying to helping patrons looking for books that were not on the expected shelf. The data gathered showed that something needed to be done NOW as more than 40% of staff time was spent on handling physical materials. This made the material management pain immediate and real. At the time, library commentators across the world were predicting that the physical book would be gone by the end of the decade, but a solution was
needed right away.
When staff started looking at possible solutions it soon became clear that off-the-shelf industrial logistics systems did not serve the purpose. The software had to be developed – earlier projects had shown that response times were crucial – slow response or delayed updates between LMS and logistics system would remove the potential benefits.
Carsten Hammershøi tells the story of how he was finally persuaded of the viability of the idea of an automated floating material handling system. While pondering about the problems, he found a case story from Lyngsoe Systems, where the Lyngsoe LIVE Logistics™ asset management helped track over 200,000 fish crates from the Danish fishing industry, knowing where all the crates were in real time, ensuring that no crates were lost on their routes between the many Danish fishing harbors.
For the IMMS™ development project, Lyngsoe Systems came forward bringing a solid track record of library automation as well as a unique logistics background forging a firm starting point for the development of IMMS™ in collaboration between the two libraries and the company.
The initial sharing of knowledge and skills between the Lyngsoe Systems developers and the libraries has grown into a continued development partnership. Every year a percentage of the license fee is set aside for new customer-led development. This ensures that IMMS™ is kept relevant for modern library needs.
“We knew from our earlier projects with Self Service that response times were crucial, slow response or delayed updates between LMS and logistics system would remove the potential benefits“.
“The introduction of the sorter and self-service returns led to extensive change of workflows throughout the library, simplifying material handling leading to a drastic fall in work related injuries from afflicting almost 100% of the circulation desk staff to 0%.”
Susanne Hansen
Aarhus Libraries
Benefits
Even distribution of floating material
When the Aarhus collections started to float at the time IMMS™ was introduced, statistics soon showed significant differences in circulation and returns from the different branches. In general, it seemed like the patrons enjoyed the large and varied collections of the main library but embraced the ease of returning locally.
This made some of the branch libraries receive a large proportion of the returns while the main library has a very high lending rate. IMMS™ regulated this automatically so all shelves throughout the system was stocked correctly at all times.
Carsten: “One of most visible advantages with IMMS™: No more overfilled shelves and no more having to move the content of an entire shelving unit to squeeze a couple of books in.”
This is where the first visible benefit of the IMMS™ real-time distribution algorithm became obvious. Had it not been for the algorithm, the main library would have emptied quicker than staff could have rebalanced, but instead, the staff was left free to focus on making the library flourish as the cultural center it was planned to be – leaving IMMS™ to keep the shelves stocked and the planned content in the right places.
Carsten: “That IMMS™ runs on generic Android smartphones makes a big difference. All staff have the IMMS™ app on their mobile phone, so all daily tasks such as registration, picking and correcting errors, can be done ad hoc when and where there is a little time. Before we got IMMS™ we spent a lot of time locating material but IMMS™ brings accordance between expectations and reality.”
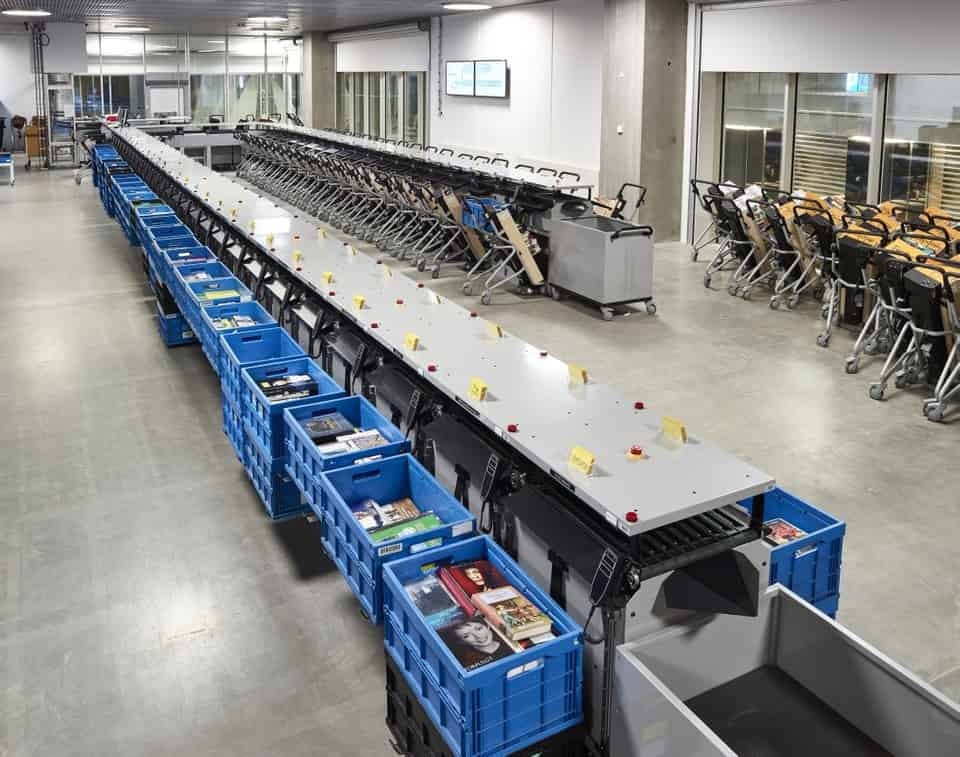
The Result
A few years later, when DOKK1 opened, this difference became even more noticeable as the Aarhus population rapidly embraced the beautiful library spaces on the harbor front. Of course, this level of automation required organizational changes and staff acceptance of handing the control to a system instead of individual branch library managers. The traditional librarian skills of knowing exactly what was on the shelves also had to be recalibrated.
Instead of relying on memory of earlier purchases, it was now necessary to search the LMS. This was not just due to the implementation of IMMS™. With material acquisitions centralized it soon became obvious that, instead of buying one copy per title per branch, having fewer copies floating freely between branches freed up money for more titles. The library now buys “pretty much everything” in Danish, and IMMS™ decides where it ends up. Of course, not all branches need it all, but instead of buying individual books for the branch, the librarians can profile the branch collections in the IMMS™ web administration module, diving deep into categories, subjects, and user profiles. This requires professional library skills as well as a deep knowledge of the population served and its’ behavior. When IMMS™ was first introduced there was a widespread fear that librarians would lose their relevance. However, with less time spent on manual handling of books, there is more time to get the content available to users just right.
IMMS™ gives library staff more time to understand the community they are serving; the focus is changed from moving books around to tweaking algorithms. Not all branches get everything – the local staff has a full say in which type of items is needed. Batch handling of items has improved the work environment significantly. Before IMMS™ items needed to be handled individually through the process from picking to the holds shelf, now they are scanned once when picked and all other processes are done in batches.

The Future
Public Libraries remain relevant
With well over 50% of the Danish population has used the public libraries in 2019 and with 89% of all library users using the collections when they visit, the public libraries have a big role in society. One of the ways Aarhus Public Library (AAKB) plans to retain the relevance of the physical library is by making the library collections more active, showcasing timely subjects or categories in a bookstore style. Some displays can move between branches, others are more seasonal, but once set up in IMMS™ such a display can be used again and again, and with IMMS™ in control of pulling in replenishments from shelves whenever an item is circulated, the display will always look fresh.
“That IMMS™ runs on generic Android smartphones makes a big difference. All staff have the IMMS™ app on their mobile phone, so all daily tasks such as registration, picking and correcting errors, can be done ad hoc when and where there is a little time.”
Carsten Hammershøi of Aarhus Libraries
Explore our Products and Solutions
Automated Material Handling
Simplify your library operations with Automated Material Handling. Enjoy faster returns, seamless sorting, and improved overall efficiency.
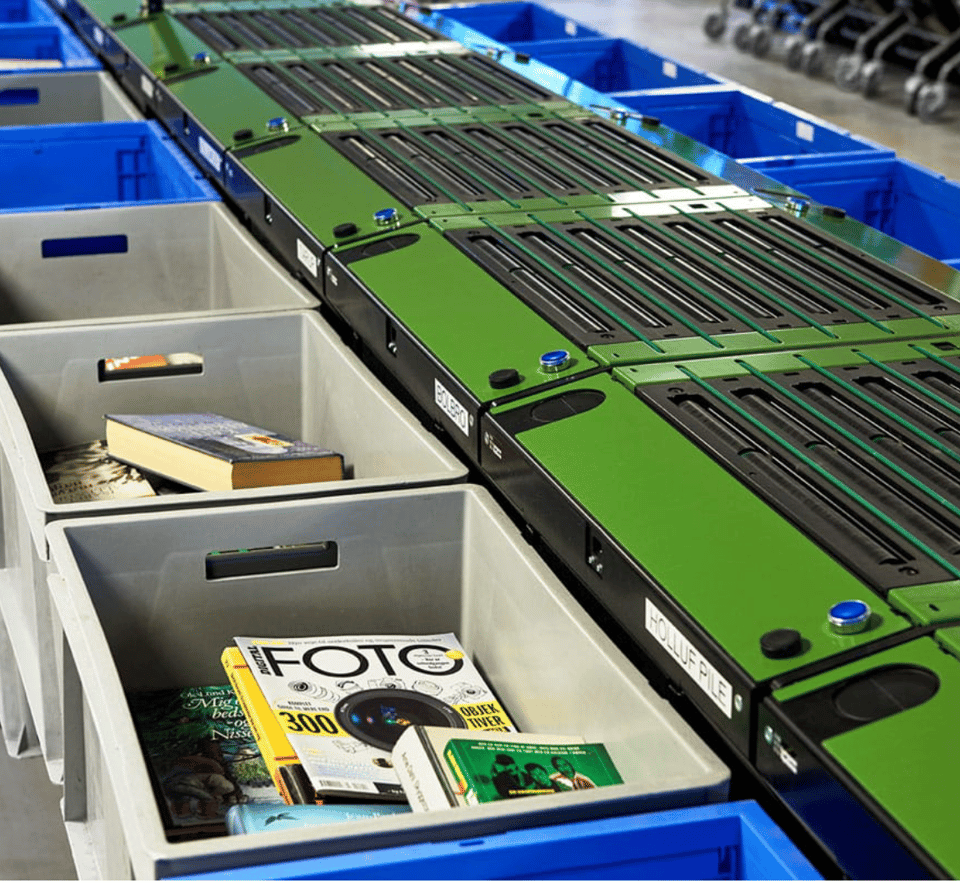
Self Service Equipment
Empower your patrons with our Self-Service Equipment. From easy check-outs to efficient returns, make every library visit a seamless experience.
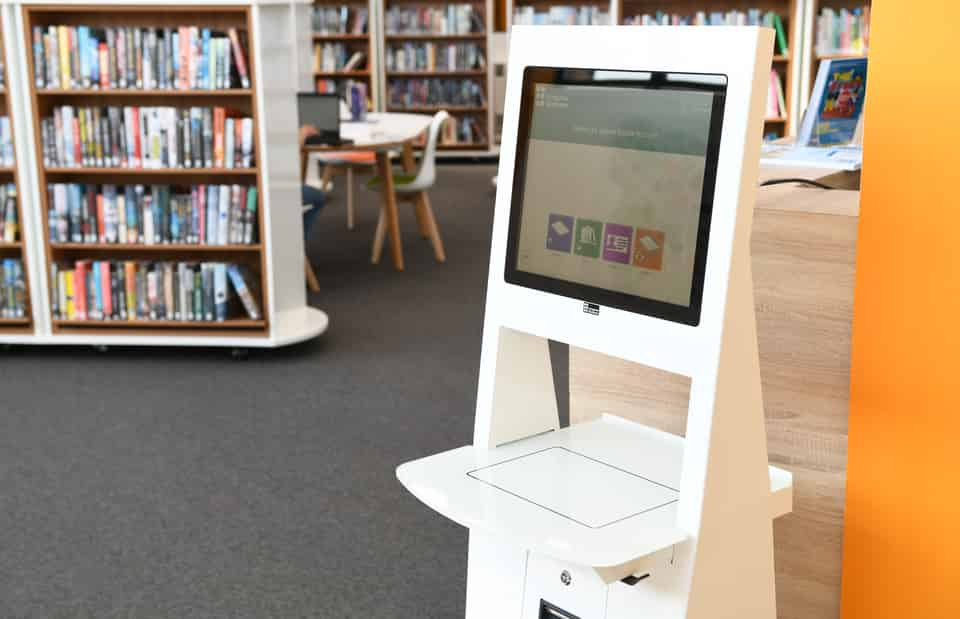
Intelligent Material Management System
Take control of your collection with IMMS. From data-driven insights to ergonomic handling, transform the way your library manages its resources.
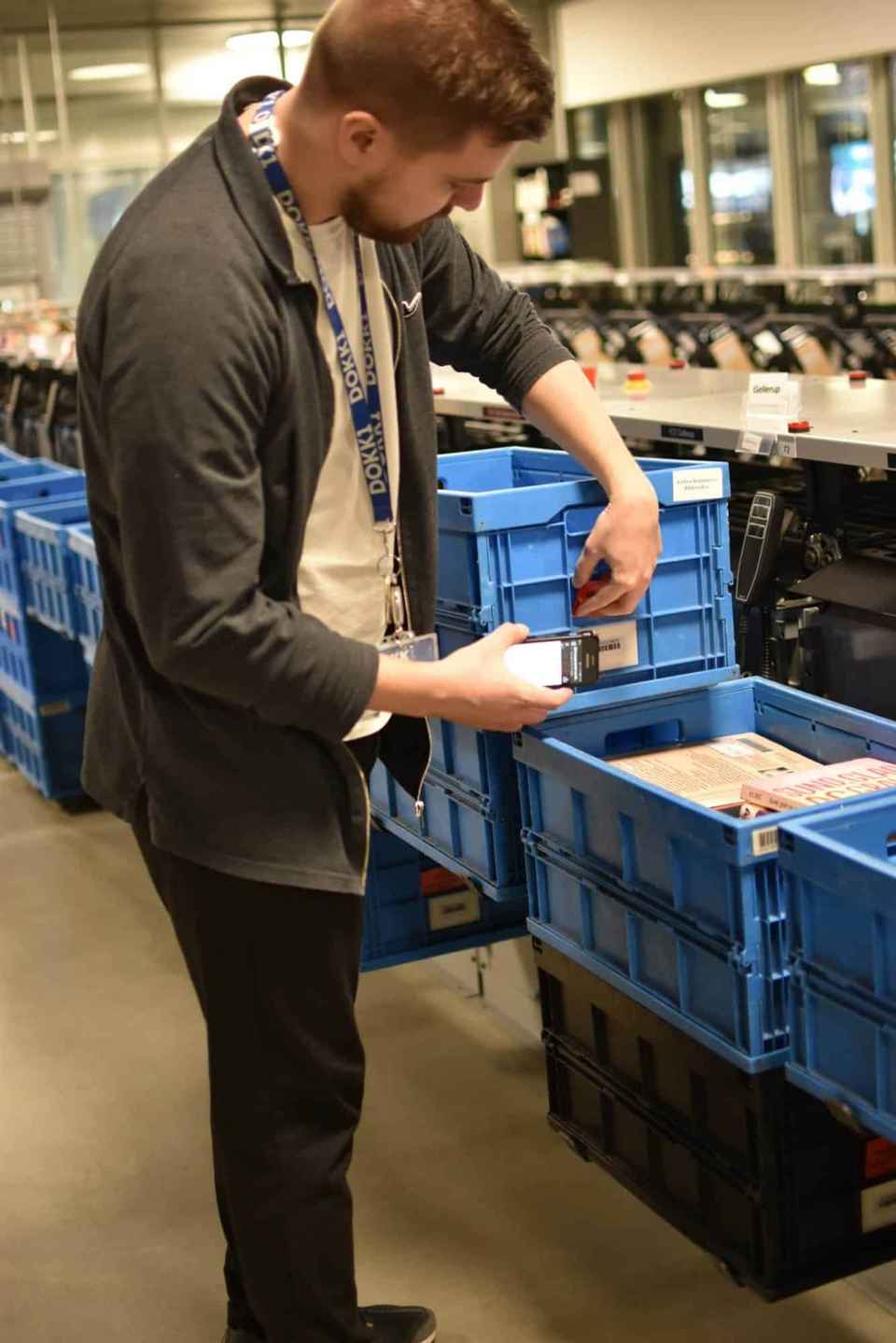