Case Story: HAVI Logistics
Operational efficiency and effective traceability
The Lyngsoe LIVE Logistics™ platform was put into operation to provide an effective tool to support warehouse and distribution processes, and provide HAVI Logistics with a real-time overview of products and shipments from producer to retailer.
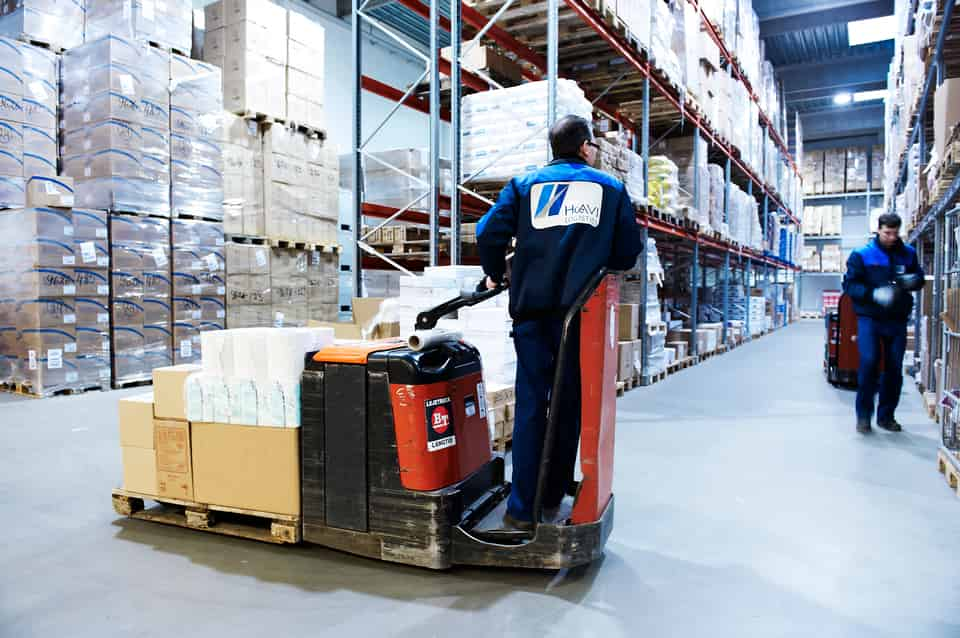
About HAVI Logistics
HAVI Logistics is a global, privately owned company focused on innovating, optimizing and managing the supply chains of leading brands. Offering services in supply chain management, packaging, logistics and recycling & waste, HAVI partners with companies to address challenges big and small across the supply chain, from commodity to customer. Founded in 1974, HAVI employs more than 10,000 people and operates more than 100 distribution centers in Europe and Asia and visits approximately 20,000 delivery points. HAVI manages the flow of products in and out of three temperature zones – chilled, frozen and dry across their network. Being able to manage the complex supply chain, operational efficiency, real-time visibility and traceability is a key requirement for success.
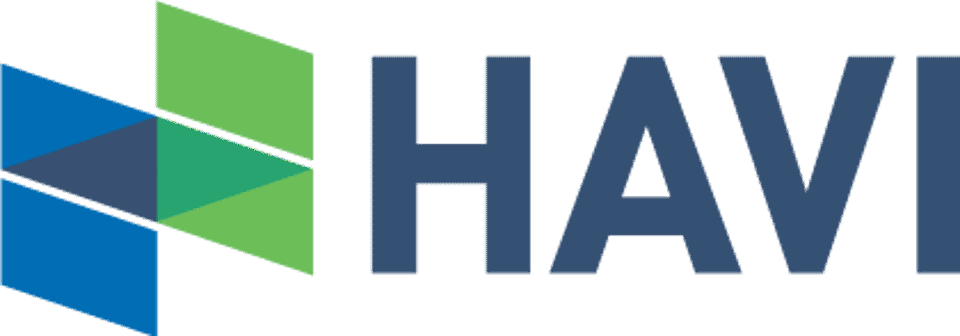
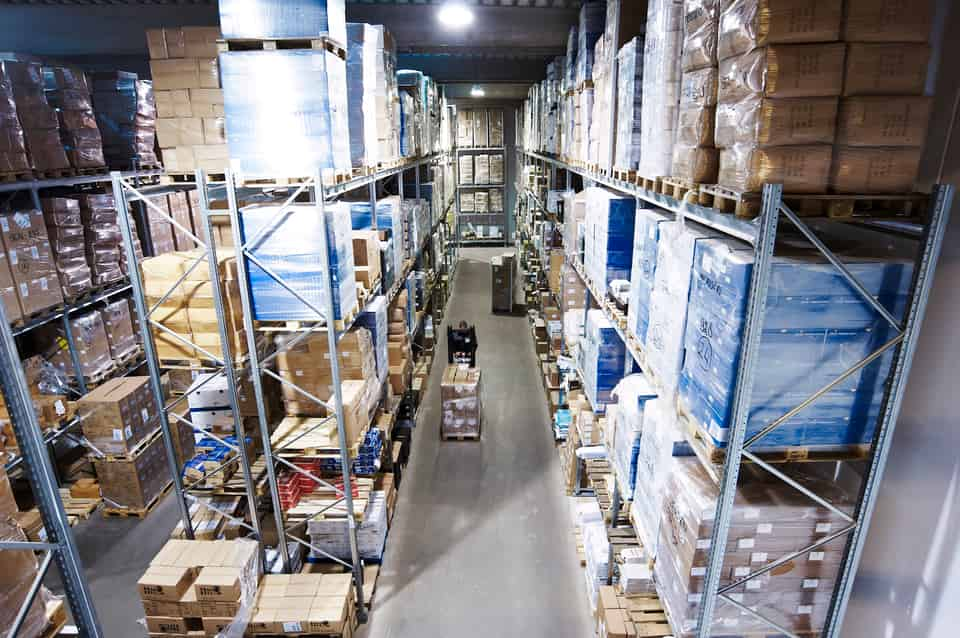
The challenge:
Quick response strategy in case of recalls
Being faced with increased food traceability requirements as well as internal demands for improved supply chain efficiency made HAVI Logistics look for a new warehouse and distribution system in 2005. The system should provide them with a quick response strategy in case of recalls, enable supply chain visibility, and be scalable to support future market expansion. Full visibility and traceability were necessary to utilize the system for continuous supply chain optimization.
The Benefits:
Increased brand protection for HAVI logistics and their customers
Complete visibility and traceability throughout a global distribution network and provided the ability to block distribution at floor level and limit the number of affected products in case of a recall.
Online documentation for food traceability and increased brand protection for both HAVI Logistics and their customers.
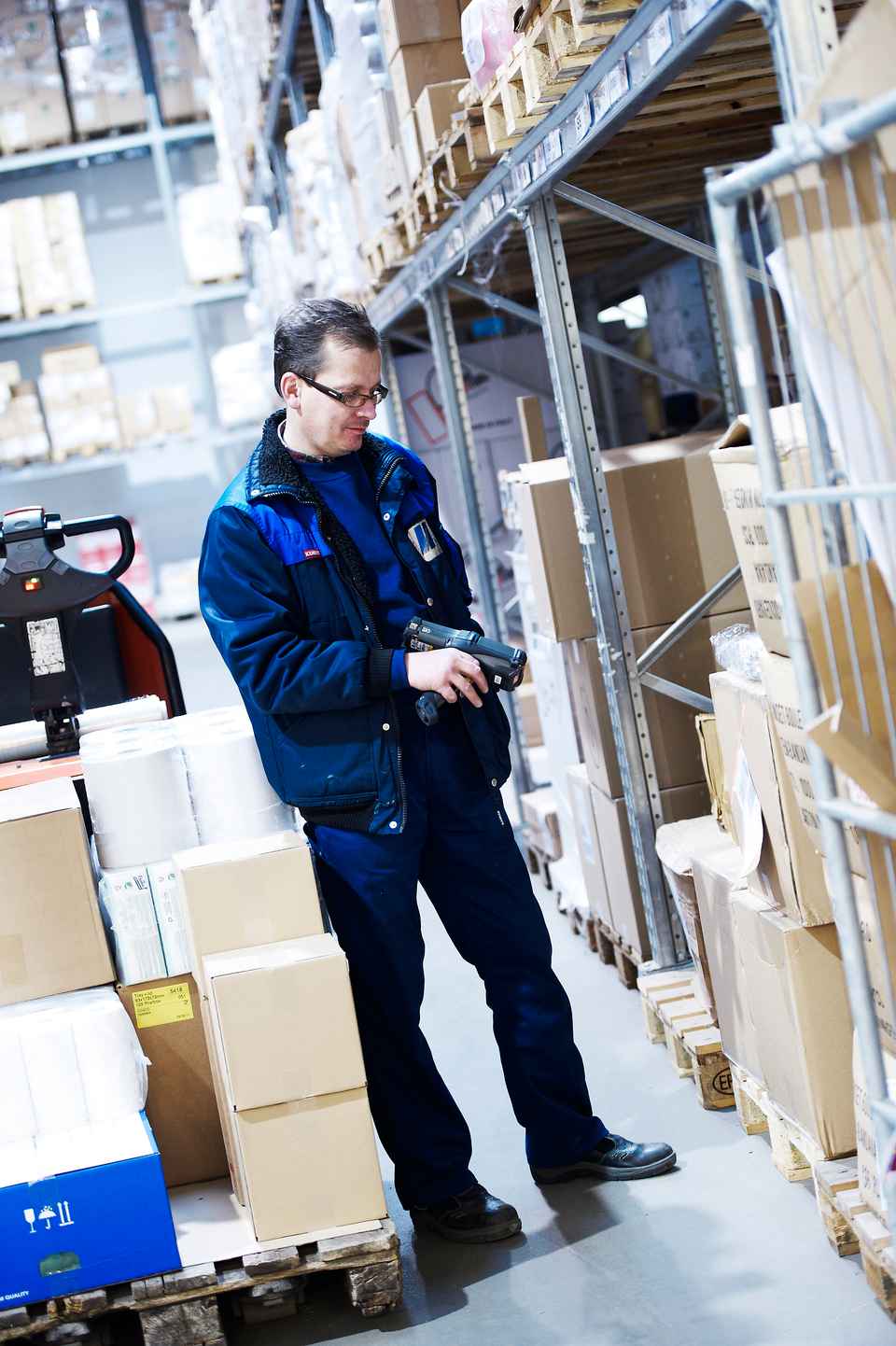
Further Results:
Full visibility and traceability
The customer has gained multiple benefits by implementing the Lyngsoe LIVE Logistics™ Platform, as the full visibility and traceability have supported them in meeting legal requirements as well as optimizing their global supply chain. They have improved the protection of their strong brands against brand value erosion and at the same time minimized consumers’ risks.
Should we help you optimize?
Contact us to learn more about how we can elevate your business.
Find More Inspiration