Case Story: BoConcept
Transforming warehouse logistics: The power of Lyngsoe LIVE Logistics™
BoConcept faced the challenge of managing several non-communicating systems. They found their solution with Lyngsoe LIVE Logistics™, our central monitoring system that optimized their logistics without downtime, ensuring reliability, and cost savings for the future.
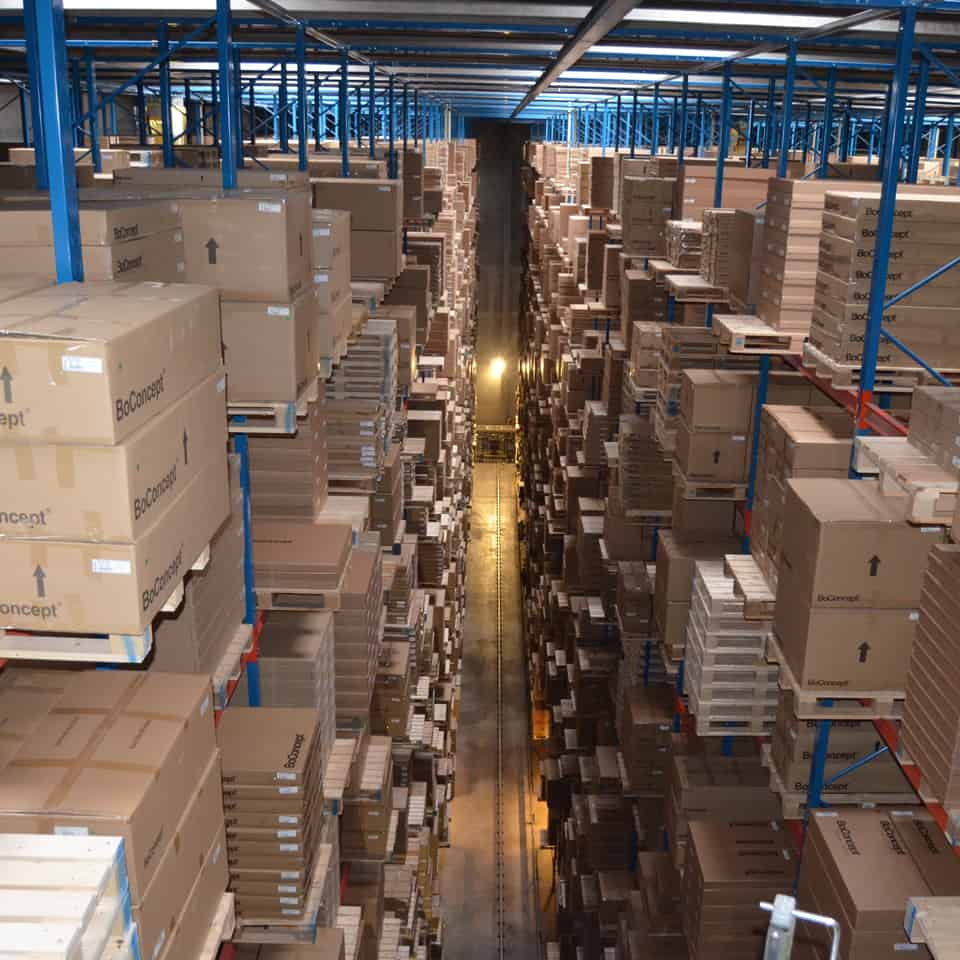
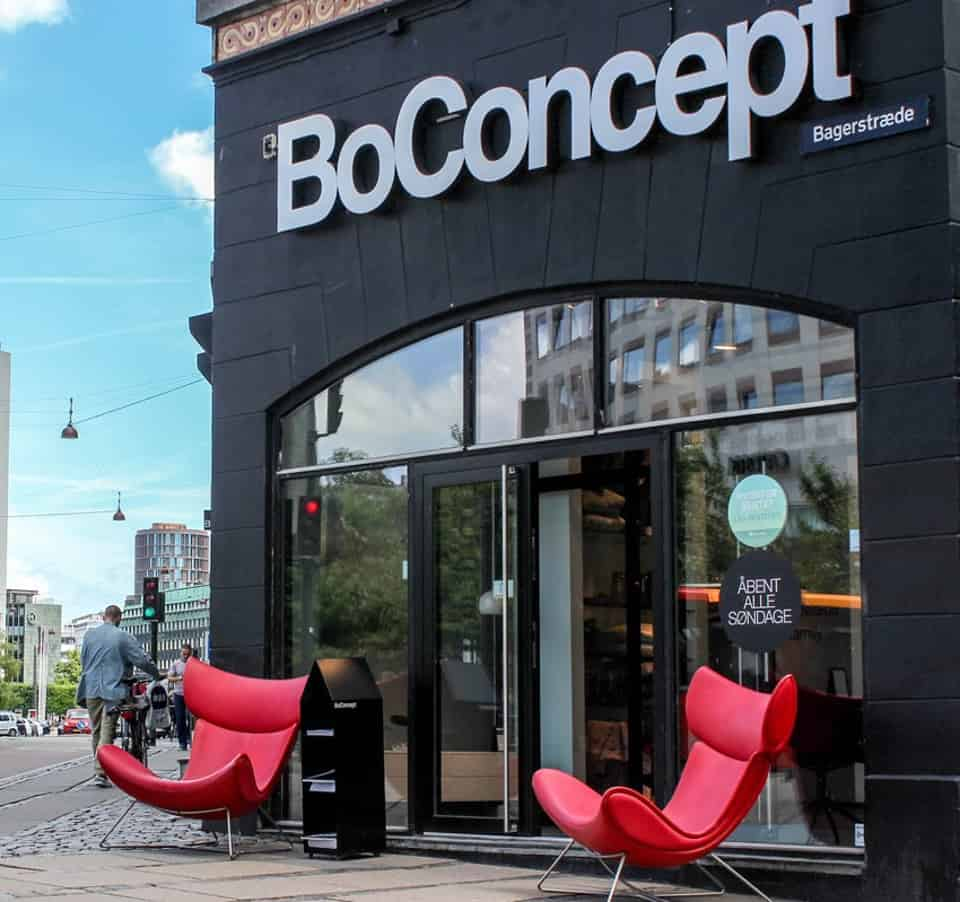
The Challenge:
Several old systems not communicating with each other
To manage material handling equipment, for example, high-bay, robots, and conveyors, BoConcept had several older systems running alongside their ERP system. None of the systems communicated with each other, making it difficult to get a clear overview and quick reaction to any mishaps. With a high risk of daily breakdowns, leading to delays, and software providers went out of business or unable to provide cost-effective updates, it was crucial to find a new future-proof solution. With evolving demands within global retail and e-commerce, their old management system had to be improved drastically, with no-stand-still during an implementation.
Our Solution:
Implementing Lyngsoe Live Logistics™ as the central monitoring system
Lyngsoe Systems was chosen as the preferred partner to optimize and create a smart, stable infrastructure for BoConcept’s logistics operations. Through a comprehensive specification phase done without supporting documentation on existing systems and interfaces, Lyngsoe Systems managed to gain control over the entire logistic flow and to implement Lyngsoe LIVE logistics™ including a SCADA solution as their central monitoring system. The material handling equipment would continue to work during and after the implementation, which was done over one weekend with two additional weeks of supervision, avoiding any downtime for BoConcept’s operations.
With Lyngsoe LIVE Logistics™ BoConcept avoided replacing their existing equipment and gained a comprehensive solution to manage all logistic processes and equipment. With now only one provider, a radical increase of reliability in operations, regular software updates, and a clearly structured overview, the project has been a great success for BoConcept saving costs on future service, upgrades, staff, and integrations.
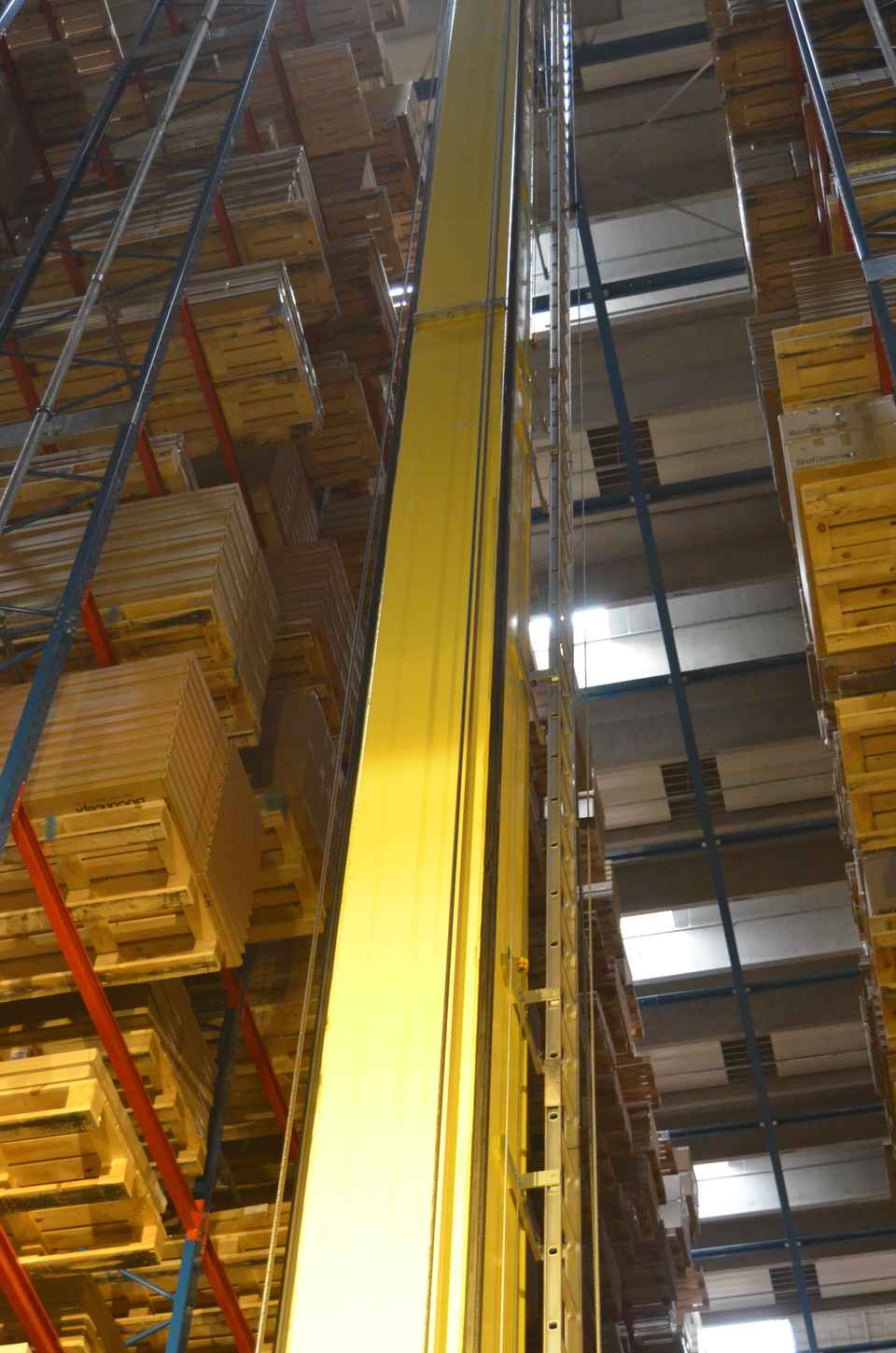
"The Lyngsoe LIVE Logistics™ WMS is an up-to-date system for our warehouses, giving us the ability to modify for future improvements, regardless of Windows or any other software changes. With a professional and friendly collaboration, we’ve achieved the best from both sides, making this a good and insightful project. We can only recommend Lyngsoe Systems as a professional and competent supplier and service provider of Warehouse Management Systems."
Jens Lønborg Andersen
System Support Warehouse & IT Projects, BoConcept
The Benefits:
A regularly upgraded software system
- Saving costs on utilizing existing assets
- Reducing the risk of crucial downtime
- A regularly upgraded software system
- No downtime during implementation
Further Results:
A solution that managed to gain control over all existing systems
The planning and close collaboration between BoConcept and Lyngsoe Systems ensured a solution that managed to gain control over all existing systems, structuring and creating a simple and stable warehouse management system. The return of investment from this was invaluable for BoConcept as the risk of not being able to do delivery because of breakdowns was unacceptable.
Do you have an outdated system?
Contact us to learn how we can find a solution without replacing your existing material handling equipment.
Find More Inspiration