Case Story: University and State Library of Tyrol
Numerous Benefits to Automating the Library Return Process
“The partnership with Lyngsoe Systems was very service-oriented. We were able to rely on the team’s professional and competent advice during both the planning and implementation of Lyngsoe’s products.”
Mag. Monika Schneider-Jakob MAS, Customer Service and Public Relations, Services for ÖBs (Head) Library Education / University Course Library and Information Studies MSc (Org. Head)
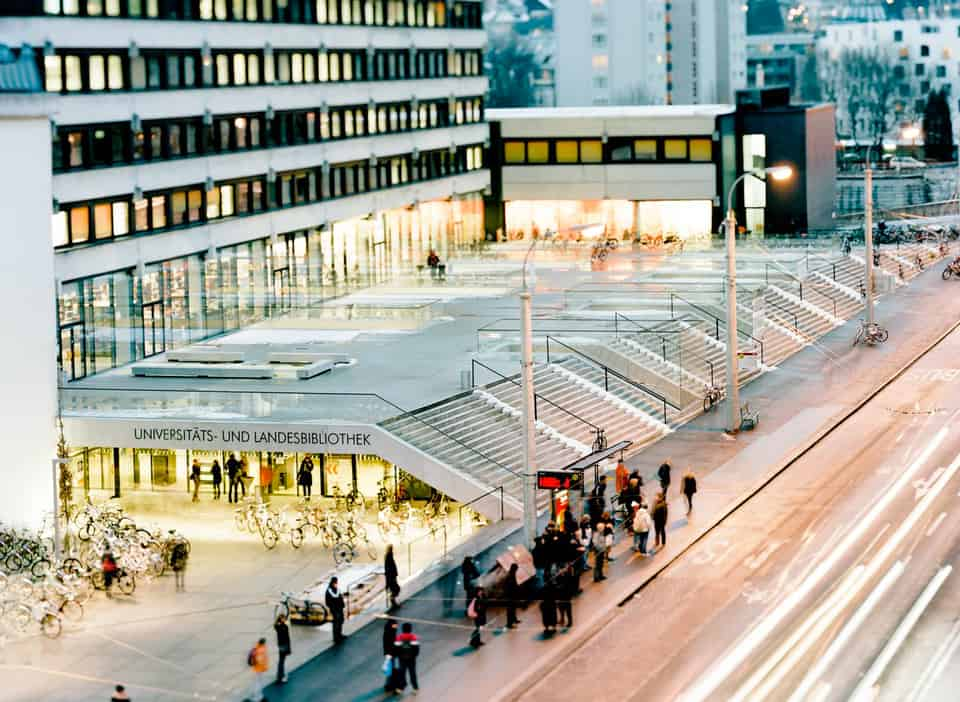
About the Library
“Material competent since 1745” – as the third largest library in Austria, the University and State Library of Tyrol supports research, teaching and studies with a wide range of physical and electronic materials and, as the Tyrolean state library, also reflects the regional literary landscape. At a total of seven locations in the city of Innsbruck, the ULB Tirol offers space for encounters and exchange and builds bridges between the past and the present. More than two million library visits and more than 350 opening days a year, make the library a central hub for knowledge, education, and information in Tyrol.
The Challenge
With the structural expansion of the main library and the construction of a 4,000 sq m new building completed in 2009, library customers were able to return materials from all seven locations of the University and State Library Tyrol (ULB Tirol) seven days a week, from 8 am to midnight, via return flaps with slides and spring-loaded book boxes. The materials were sorted and returned to shelves manually by library staff, then confirmation of the return was sent by e-mail with a time delay. Despite multiple in-house optimizations of the process, the solution was unsatisfactory in the longterm from a logistical and ergonomic point of view. Library staff had desired an automated and thus more efficient and streamlined procedure for a long time.
The Solution
An adaptation of the procedure had to meet financial, structural, fire safety, user-friendly and library requirements. In collaboration with Lyngsoe Systems and, after an extensive review and planning process, we recommended that the return flaps should be replaced by two Lyngsoe Library Mate™ 1200 return kiosks. Thanks to the connected Lyngsoe Sort Mate™ 2000 sorting system, with ten sorting destinations, eight of which are for Lyngsoe Ergo Trolleys™, one for Lyngsoe Ergo Box™ and a dump, the returned materials are now sorted into sorting containers according to departmental libraries and the main storage library. A beacon in the counter area immediately informs the service staff about the current return status and the need to empty the trolleys.
Benefits
The system, which went into operation at the beginning of 2018, makes the daily routine of the library considerably easier:
- Work processes that previously required a lot of staff could be streamlined. The automatic return and subsequent sorting by location of the individual materials was just as popular with the staff as the ergonomic way of working.
- For library customers, automation has the advantage of faster availability of materials, immediately receiving the receipt and the
possibility of returning materials outside of the regular library opening hours. - In addition, the material-friendly return process ensures fewer repairs or new purchases and thus also decreases expenditure.