Precision Control in Lyngsoe Sort Mate™ 2000
Why do precision control?
Lyngsoe Systems prioritizes precision control in the sorting process of our Sort Mate™ 2000 library sorters. This means that our customers will experience a minimal need to monitor the systems, as items are sorted correctly every time. Though it may sound as an insignificant feature, it has far-reaching benefits for libraries.
Precision Sorting
The precise control is enabled through several components: photoelectric sensors, encoders, and the advanced Lyngsoe software. It is in the intelligent combination of these inputs that precision is achieved.
High-quality motors and belts ensure items land exactly where they need to be. By tracking the motor's rotation with encoders and combining that with photoelectric sensors that measure the time items pass over them, we can accurately determine the length of any given item.
This information, along with the item's position relative to the photoelectric sensors, allows us to precisely control where it is discharged. Discharge is achieved by raising and activating rollers on either side of the conveyor belt. Although it happens too quickly to see clearly, the belts and rollers are speed-controlled, allowing for precise acceleration and deceleration to further refine item movement.
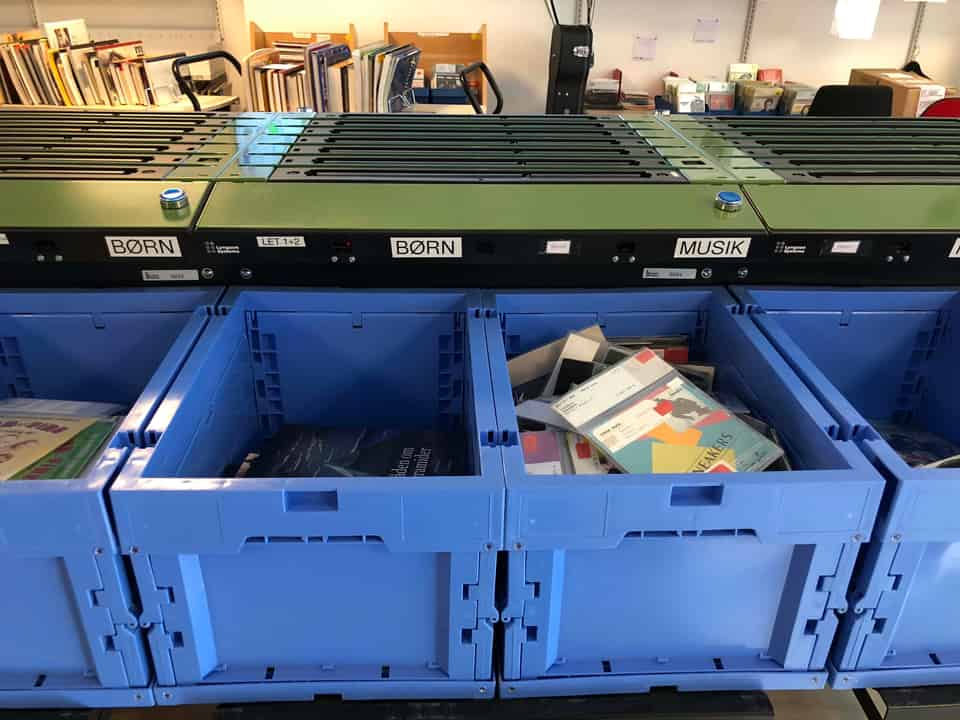
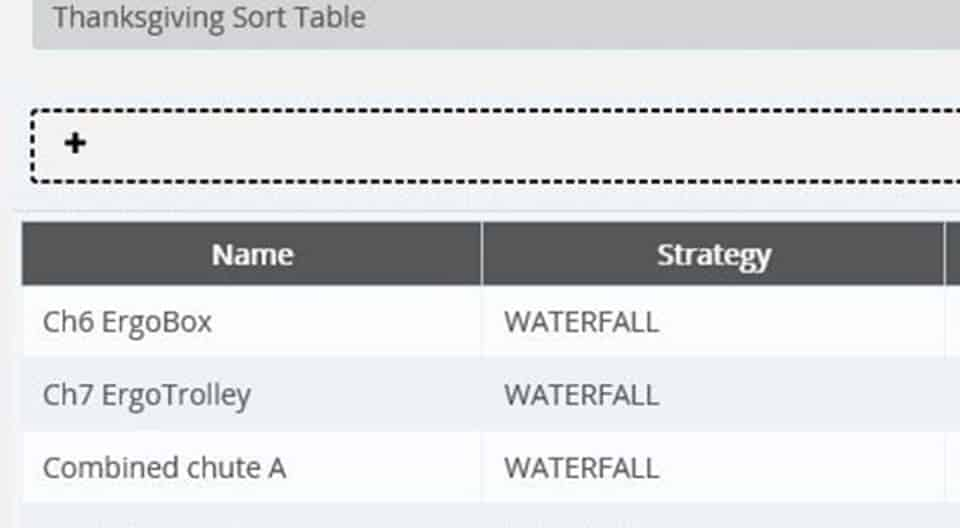
Real-time Tracking for Reliable Sorting with Lyngsoe Sorter Controller™
The Lyngsoe Sorter Controller™ (LSC), working in conjunction with these other inputs, maintains real-time tracking of library items and destination availability. This enables real-time decision-making, ensuring reliable feedback on whether items were sorted as expected or why they may have been diverted to alternative destinations to maintain continuous sorting.
The LSC can even backtrack on an item level if something unexpected occurs. For instance, if an item is sorted to the wrong destination, the LSC can often identify the issue as a simple error in the sort table, which can be easily corrected. Alternatively, if a destination is full, the LSC may send the item to an exception bin to keep sorting running smoothly while the full destination is emptied.
Why Precision Sorting Matters
Precise discharge and intelligent sorting significantly reduce the need for constant physical monitoring of an AMH system. Without precise control, items often land in the middle of modules, creating piles that require manual adjustment by library staff. This can increase labor requirements by up to three times compared to distributed discharge.
Precisely centered sorting is crucial for creating stable, vertical stacks in stacking carts like the Lyngsoe Ergo Cart™. This ensures stacks remain stable during both the sorting process and the transportation to shelves, reducing the risk of damage. The Ergo Cart's design, including its patented squeeze function and offset backplate, prioritizes ergonomic comfort for library staff.
The combination of precise sorting and photoelectric sensors allows a single sorting module to be divided into two destinations. This is particularly useful for handling smaller item groups like DVDs without requiring additional modules. If the need for separation diminishes, the split chute can be easily combined into a single logical destination within the Lyngsoe Sorter Controller™.
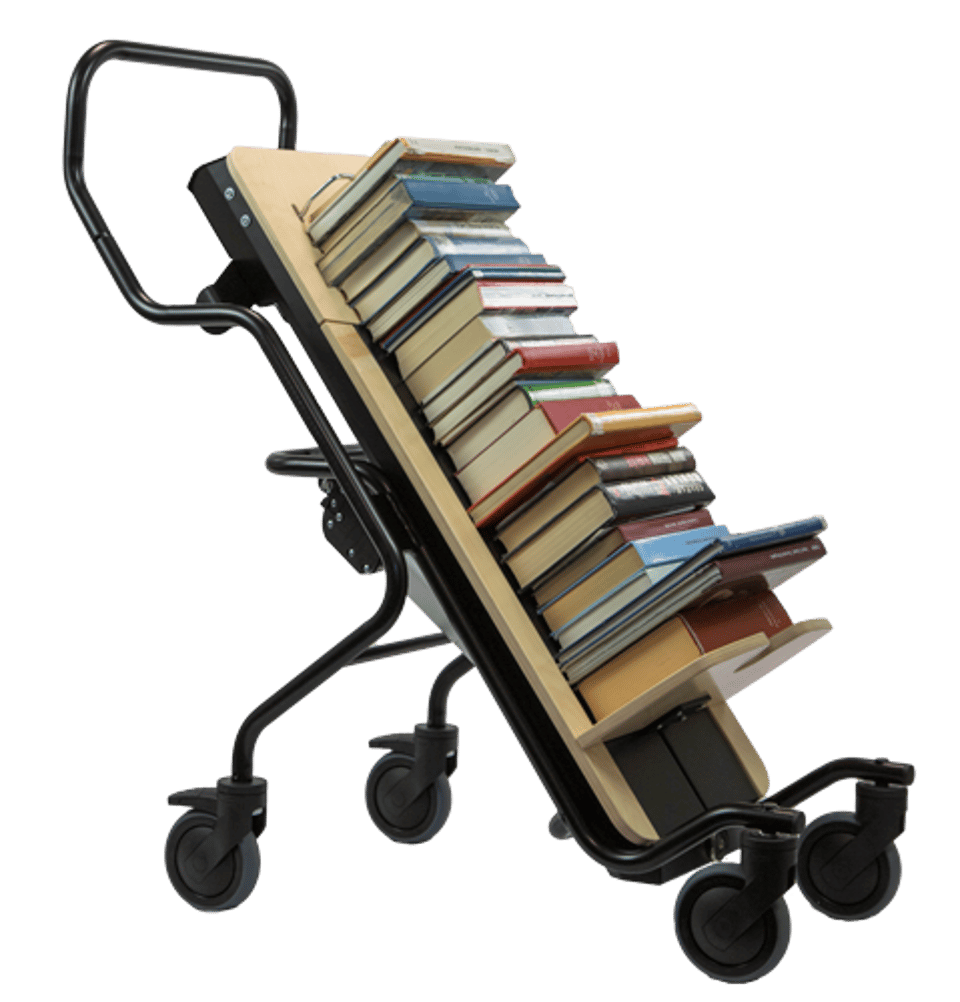
Other Precision Control Benefits
Precision control becomes increasingly crucial as sorters grow in size. Without accurate control and tracking, incorrect discharges will inevitably occur. These mis-sorts lead to increased manual handling, intervention, and labor demands.
Dividing long and short items into logical destinations is an effective way to maximize available capacity. For instance, you can create a logical destination with two physical destinations, assign them to children's books, and observe how longer items form perfect, ready-to-shelf stacks in one cart while shorter items do the same in the other or are placed in an Ergo Bin™.