In a fast-paced logistics environment, efficiency is particularly important. One of the key components to delivering this efficiency is having a streamlined process for the return and maintenance of returnable transport items (RTIs). At Lyngsoe Systems we understand the critical role that RTIs play in maintaining an effective supply chain. We have found that by leveraging our advanced Radio Frequency Identification (RFID) tracking solutions, businesses can significantly enhance the management of RTIs and extend their lifecycle, leading to increased operational efficiency, reduced costs and improved sustainability.
In this article we explore how RFID technology can maximize the efficiency of RTIs and transform logistics operations.
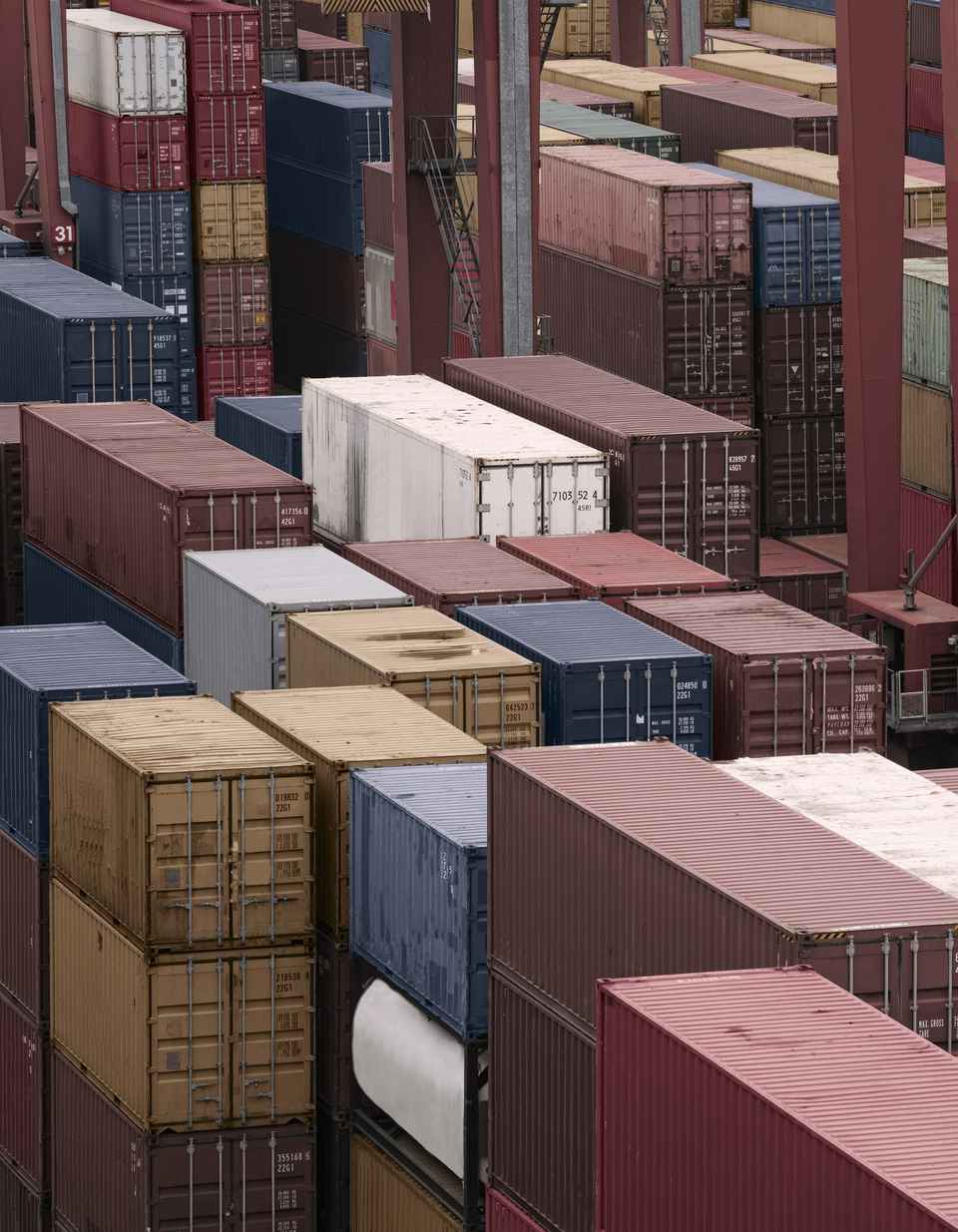
Understanding the value of RTIs
Returnable transport items, such as pallets, crates, containers, and trolleys, are essential assets in the supply chain. They facilitate the safe and efficient movement of goods from suppliers to retailers and back again, but their true value is often overlooked. Managing these items can be challenging due to their constant movement and potential for loss - both geographically and financially. Outdated manual processes only serve to heighten these problems.
This was the challenge faced by Pack & Sea A/S, a collaborative venture between ten Danish fishing ports, who were facing substantial losses without a way of being able to easily track and retrieve the over 350,000 fishing crates they have in regular use.
Our own system Lyngsoe LIVE Logistics™ offered a solution to these challenges. By attaching RFID tags to their RTIs, they are now able to automatically and accurately track the location and status of each item in real-time. This not only streamlined operations, but also provided valuable data insights that are driving further improvements.
At Lyngsoe we offer comprehensive RFID solutions tailored to the unique needs of logistics and supply chain operations. For Pack & Sea A/S we designed two UHF RFID tags that would uniquely identify each fish crate. We select and test RFID tags that are designed for durability and reliability, ensuring they can withstand the rigors of constant use and in combination with our own software platforms provide seamless integration with your existing systems, delivering real-time data and insights for optimized RTI management.
The benefits of using RFID tags for RTIs
Most understand the value of using RFID for goods being stored and transported, but the mode of transportation itself is often neglected which can be a costly mistake. Here are just a few of the benefits of using RFID tags on RTIs:
Enhanced visibility and control
RFID provides real-time visibility into the location and status of each RTI. This eliminates the need for manual tracking, reduces errors and ensures that these valuable assets are always accounted for.
Streamlined operations
Automated tracking of RTIs speeds up various processes within the supply chain. This includes faster check-ins and check-outs; quicker inventory counts and more efficient sorting and dispatching.
Data-driven decision making
RFID technology generates a wealth of data on the usage, movement, and condition of RTIs. This data can be analyzed to identify patterns, optimize routes and predict maintenance needs.
Improved sustainability
Effective management of RTIs contributes to sustainability efforts by reducing waste and promoting reuse. RFID tracking ensures that items are returned and reused efficiently, minimizing the need for new resources.
Extending the lifecycle of RTIs
Wireless technologies such as RFID, BLE and GPS allow for real-time tracking and monitoring of RTIs. This provides constant visibility into the location and status of each item throughout the supply chain. Constant tracking reduces the risk of loss or theft, ensuring RTIs are returned and reused rather than being prematurely replaced. RFID systems automate inventory counts, providing accurate data on the number and condition of RTIs in circulation, allowing you to ensure that RTIs are rotated efficiently, distributing wear and usage evenly across all items.
Wireless technologies equipped with IoT sensors can even help you extend the lifespan of your RTIs, enabling you to monitor their condition by collecting data on factors such as usage frequency, temperature, and impact – allowing you to predict when maintenance is needed. The ability to plan when to make proactive repairs to minor issues before any major ones arise ultimately extends the lifespan of the RTIs.
The recovery process for RTIs is just as important as the tracking and maintenance elements, ensuring these assets are quickly and efficiently returned to the point of origin (or to a maintenance facility). Having an efficient return process ensures they are available for reuse sooner and this reduced turnaround time minimizes the need for purchasing additional RTIs to meet demand, lowering your overall costs.
By extending the lifecycle of your RTIs you are also having a positive environmental impact, as by reducing waste and the need for new materials you will be generating a lower carbon footprint.
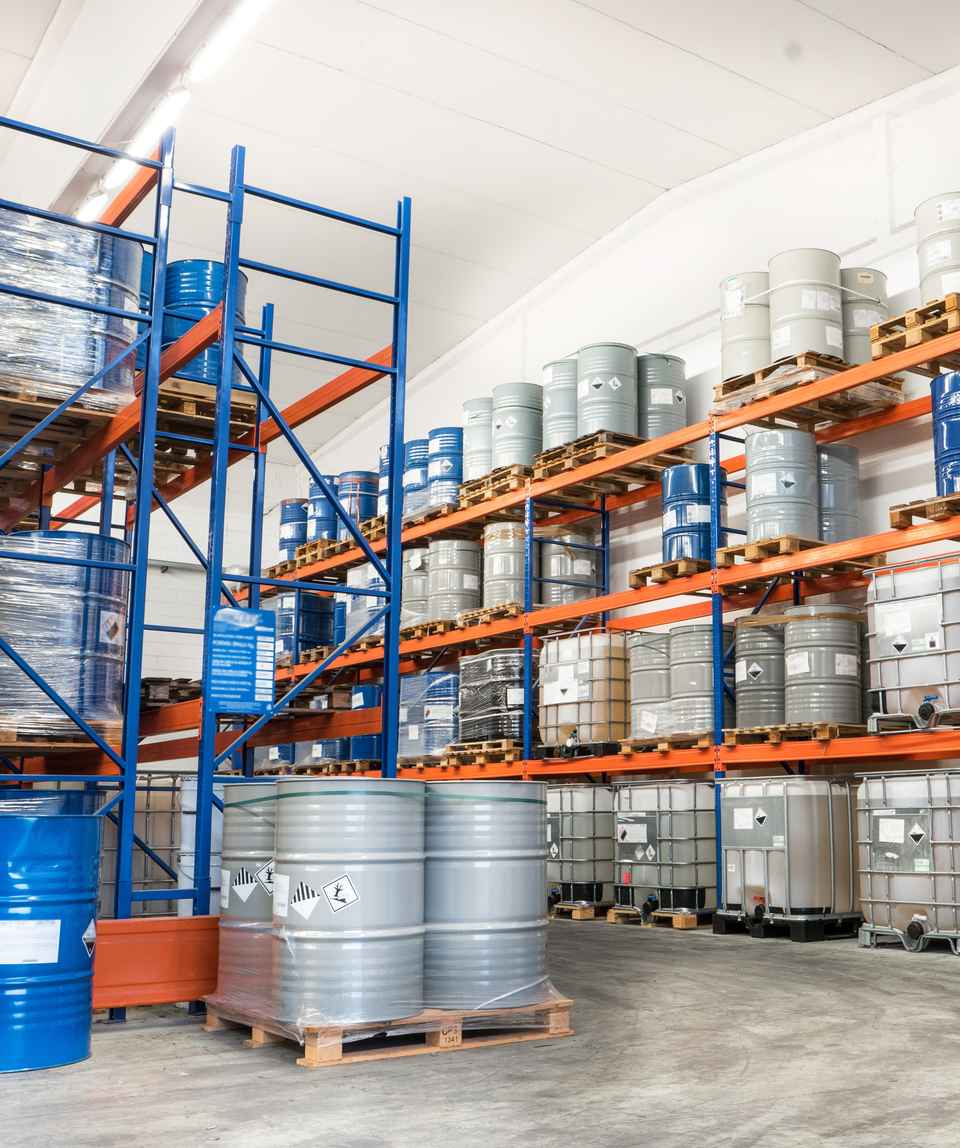
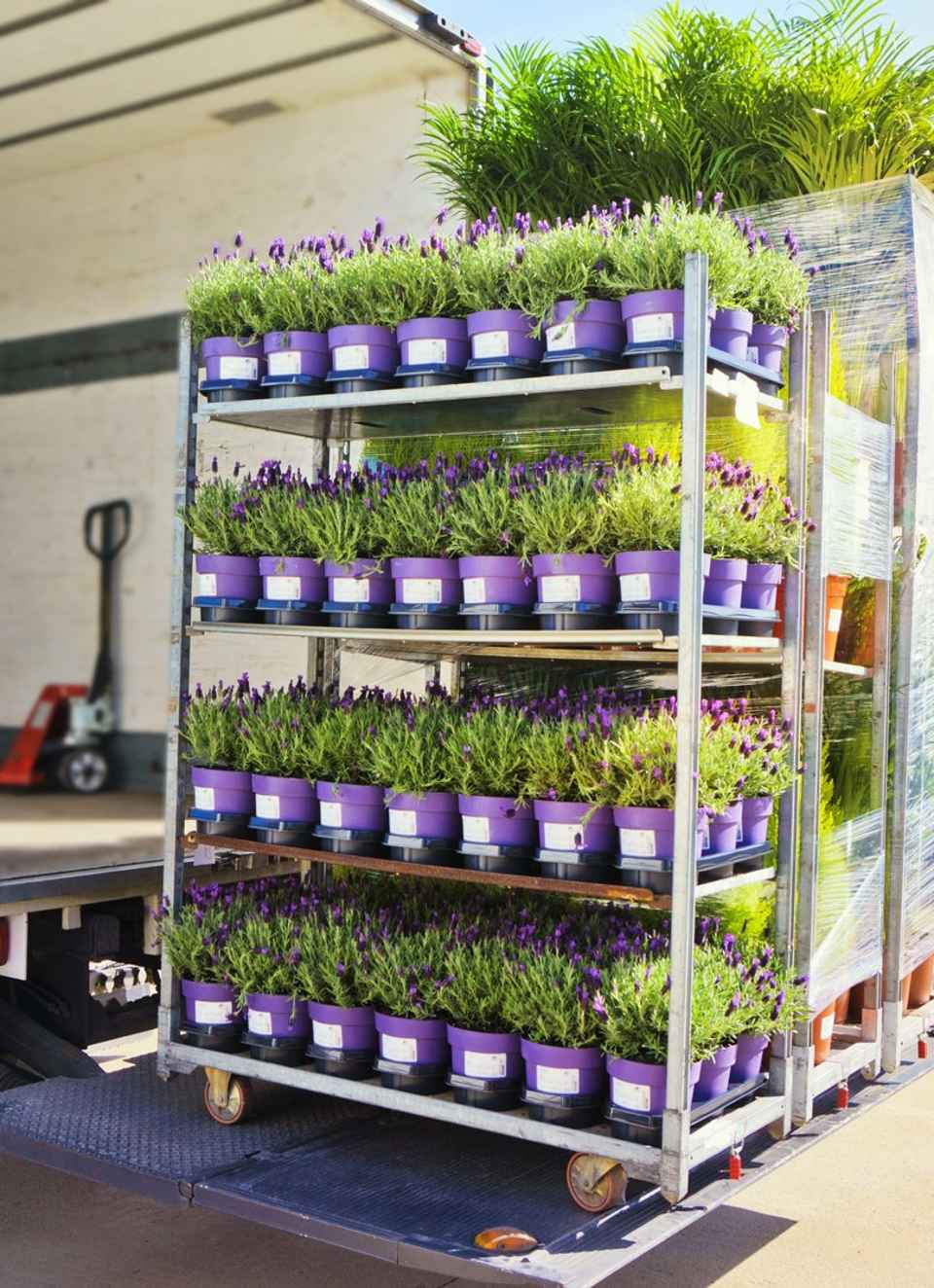
Success in action
Another of our clients, Container Centralen (CC) is a pioneering company specializing in the management and pooling of RTIs within the horticultural and retail industries. They have over 23,000 users handling four million RTIs including crates, containers and trolleys. Due to the sheer volume of RTIs involved these represent a significant value to the business, so the ability to track and safely return these assets is key.
CC were keen to streamline logistics and improve efficiency across their supply chain, and found their previous solution required too much time to read and authenticate. We partnered with Omni-ID to build a tag to meet their specific requirements of a non-removable, tamper evident and quick-to-read tag that would remain effective even when exposed to water or extreme heat due to the nature of their goods.
By transitioning over to these new custom-designed RTI tags, they achieved:
- A significant reduction in reading times and increased reading range
- Increased security measures with tamper-evident features
- A design that functions in harsh conditions, giving dependable results regardless of the environment
- The ability to provide 100% verification of genuineness
- A hassle-free installation and operation process, with the convenience of using standard RFID readers
Transforming RTI management with Lyngsoe Systems
It’s clear how transformative RFID-tracked RTIs can be for logistics and supply chain management. We have demonstrated how our technology can be used to significantly extend the lifecycle of RTIs through enhanced tracking, predictive maintenance, and improved handling, ensuring they remain functional, cost-effective assets. By leveraging our advanced solutions, you can achieve greater efficiency, sustainability, and cost savings, ultimately enhancing your overall operational performance.
Get in touch to explore how we can work together to transform your RTI management.
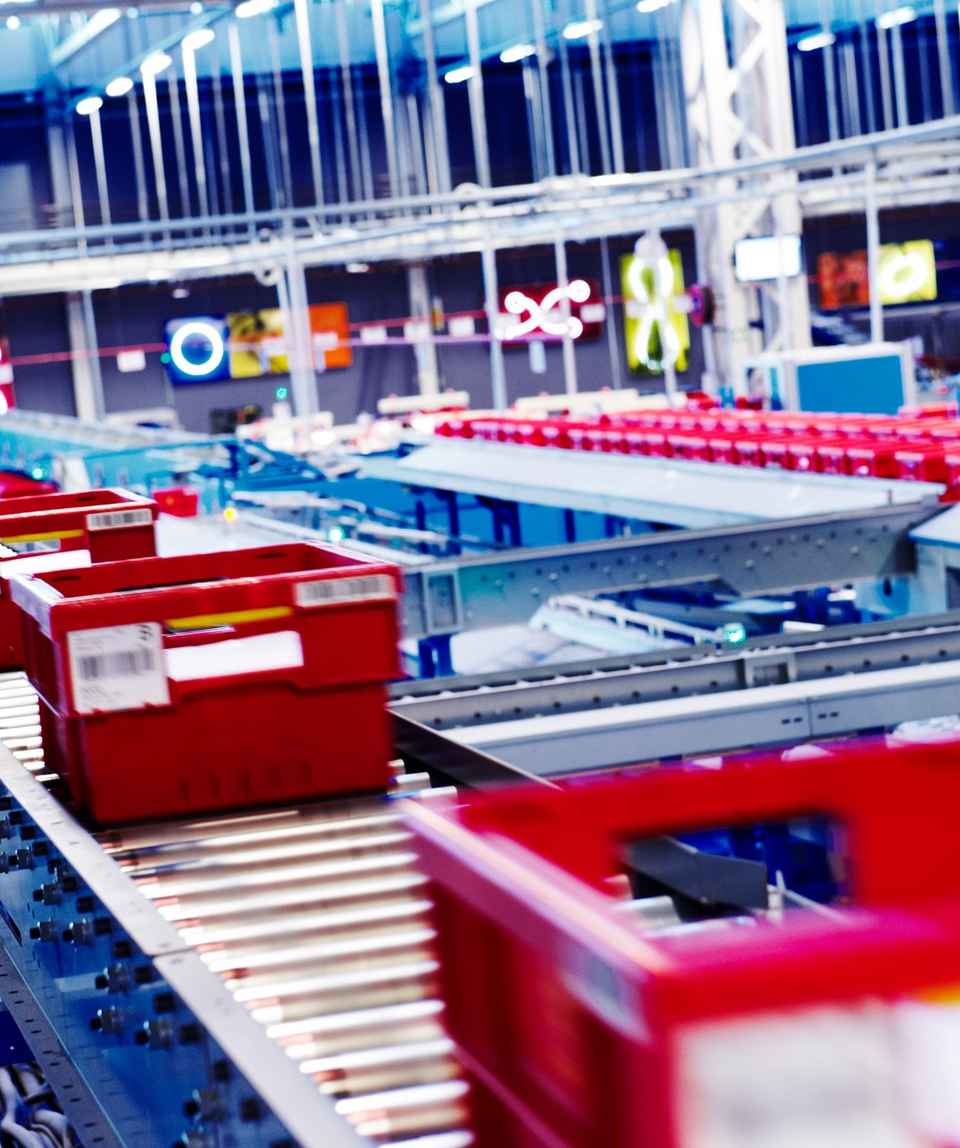
Explore Our Solutions
FAQ
How does RFID technology enhance RTI management?
RFID enables automatic identification and tracking of RTIs via tags and readers, enabling organizations to monitor asset movements, ensure accurate inventory management and reduce manual errors.
What considerations are important when selecting RFID tags for RTIs?
Consider things like durability (tags need to withstand environmental conditions), attachment method (ensuring secure attachment to various materials) and read range (for distance and frequency).
How will I see a return on investment (ROI) for implementing RFID in RTI management?
We typically see organizations experience significant ROI through areas such as reduced RTI loss, labor cost savings and operational efficiency.