Key Challenges in Modern Warehouse Operations
Proactive Solutions for Minimizing Downtime in Warehouse Operations
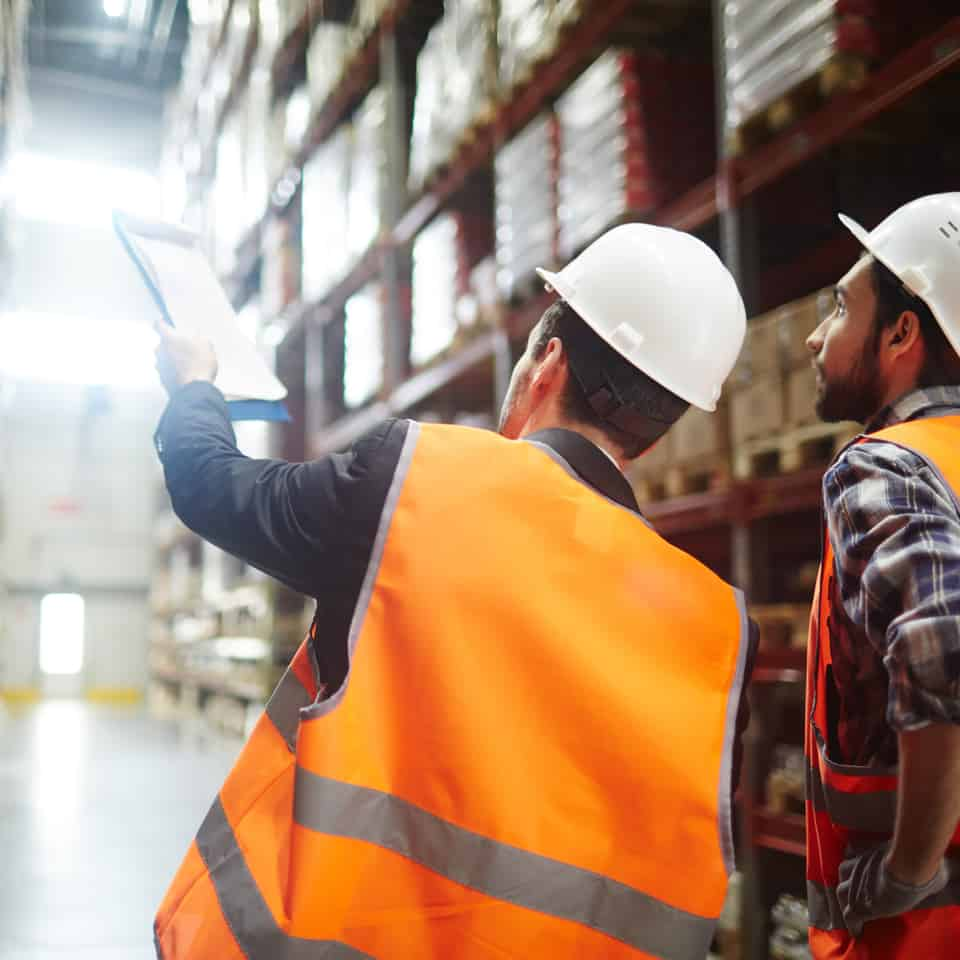
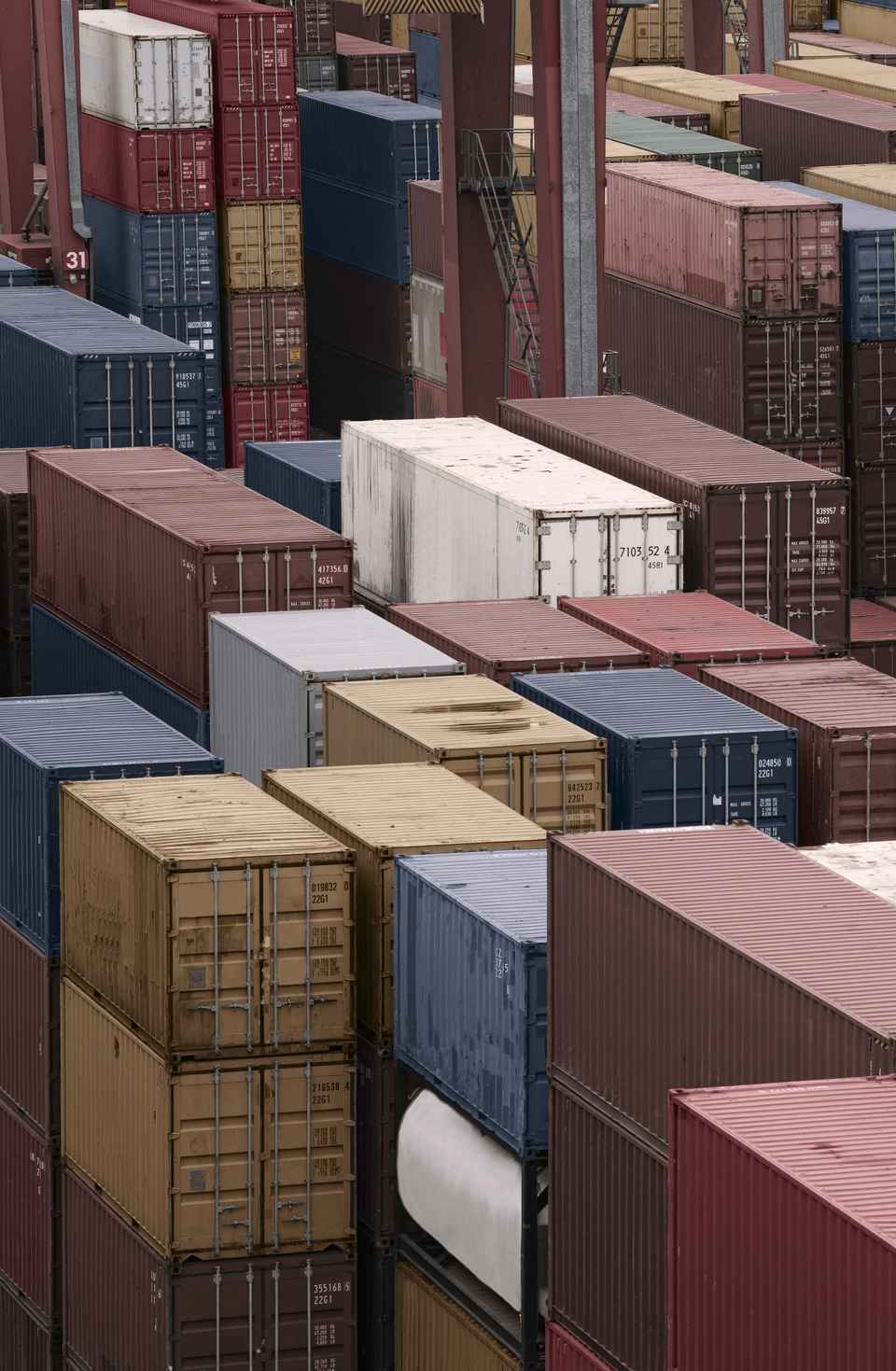
Identifying the Causes of Warehouse Inefficiencies
So, what causes warehouse inefficiencies in the first place? Some of the biggest culprits are delayed shipments, misplaced inventory, and tedious manual data entry. These inefficiencies don’t just delay orders - they also lead to wasted resources, employee frustration, and unnecessary costs. With studies showing that downtime can cost businesses as much as $260,000 per hour, addressing these issues isn’t just smart; it’s essential.
The impact of these disruptions goes beyond the warehouse walls. Delayed orders erode customer satisfaction and loyalty, while labor costs climb due to overtime. By utilizing tools like RFID tracking, real-time data visualization, and predictive analytics, our solutions help warehouses spot potential issues early on. This enables a quick response, allowing resources to be reallocated or shipments rerouted as needed. Automating repetitive tasks also cuts down on human error, accelerates workflows, and provides actionable insights for better resource allocation.
Proactive Solutions for Minimizing Downtime in Warehouse Operations
Enter Lyngsoe Systems’ Smart Warehouse solution. This solution take the guesswork out of warehouse operations, offering real-time data and automation that deliver visibility into asset location, movement, and status. This means warehouses can stop waiting for problems to happen and start anticipating them. Continuous monitoring and predictive analytics provide an early warning system, helping teams prevent disruptions and minimize downtime before they escalate into major issues.
With Lyngsoe’s Smart Warehouse solutions, organizations can implement strategies like predictive maintenance, dynamic inventory control, and continuous system updates. Automated asset tracking and predictive analytics work together to minimize downtime, keeping warehouses running smoothly and avoiding costly disruptions.
How Lyngsoe LIVE Logistics™ Optimized BoConcept’s Logistics Operations
For example, we assisted BoConcept with streamlining their logistics operations. Without any existing documentation on their systems, we completed an in-depth assessment and took full control of BoConcept's logistics flow by implementing Lyngsoe LIVE Logistics™, including a SCADA solution for centralized monitoring. This complex integration was executed with precision, during a weekend, ensuring BoConcept’s operations continued without a hitch.
With Lyngsoe LIVE Logistics™, BoConcept didn’t just get a new system; they gained a centralized logistics platform that increased reliability, reduced downtime and bottlenecks, and offered a modernised approach to an industry pain point. This end-to-end solution has also given them a robust system overview, translating into significant savings on future upgrades and labor requirements.
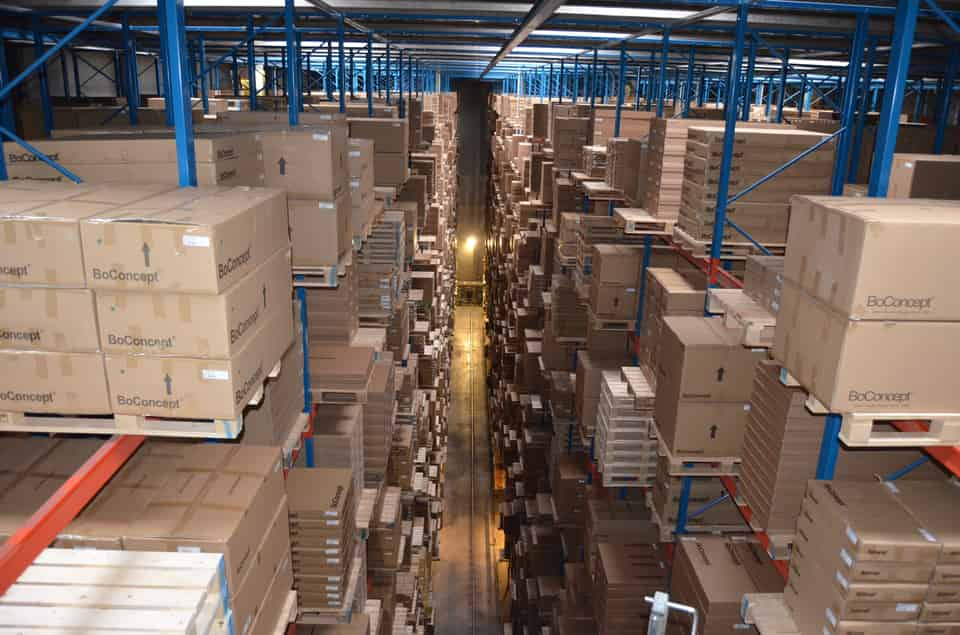
For example, we assisted BoConcept with streamlining their logistics operations. Without any existing documentation on their systems, we completed an in-depth assessment and took full control of BoConcept's logistics flow by implementing Lyngsoe LIVE Logistics™, including a SCADA solution for centralized monitoring. This complex integration was executed with precision, during a weekend, ensuring BoConcept’s operations continued without a hitch.
With Lyngsoe LIVE Logistics™, BoConcept didn’t just get a new system; they gained a centralized logistics platform that increased reliability, reduced downtime and bottlenecks, and offered a modernised approach to an industry pain point. This end-to-end solution has also given them a robust system overview, translating into significant savings on future upgrades and labor requirements.
Explore Our Solutions
FAQ
What role does staff training play in minimizing operational disruptions?
Well-trained staff are crucial for efficient warehouse operations. Regular training ensures employees are adept at using equipment, following protocols, and adapting to new technologies, reducing errors and downtime.
Can warehouse layout impact the occurrence of bottlenecks?
Yes, an inefficient warehouse layout can lead to congestion and delays. Optimizing the placement of inventory, equipment, and workstations facilitates smoother workflows and reduces the likelihood of bottlenecks.
How does predictive maintenance contribute to reducing downtime?
Predictive maintenance involves monitoring equipment conditions to foresee potential failures. By addressing issues before they escalate, warehouses can prevent unexpected breakdowns and maintain continuous operations.